Last Wednesday we discovered that some of the magnets in the chess pieces was put in the wrong way (facing downwards instead of upwards against the design on the top). So, I had to remove the bottom plate from the chess pieces and turn the magnets around. Due to the top pieces (design form an open source) having a thin material thickness, some of them broke when I removed the bottom plates and I had to print new pieces. Once the printing was finished, I just had to glue the bottom to the top. Everything should be in the right order now, but I will test them again next Wednesday just to be sure that every magnet is facing the right way (upwards toward the design).
Alongside the job with the chess pieces, I completed the design of the rotary base for the arm. I had some small issues with the design when I was finished, and had to get help from Richard to understand what I was doing wrong.
I have had to remake the design of the rotary base, I originally planned to use cycloidal gears to make the base. But I struggled to find a ball bearing large enough for the design, so I have had to remake the design using spur gears instead.
When designing the spur gears, I started to look into the math for the gears in hopes of making two gears that would work together well enough. And not having to deal with some of the negative drawbacks that traditional gears tend to have, i.e. backlash, wrong ratio value between the two gears, etc. The math is proving to be really difficult, but I will continue with this through the weekend.
I have also updated the measurements on the arm, in regards to screw and hole measurements. And to be sure that I made the holes small enough to make threads with the screws, I created and printed a test piece with different hole measurements, and testet the different holes with real screws.
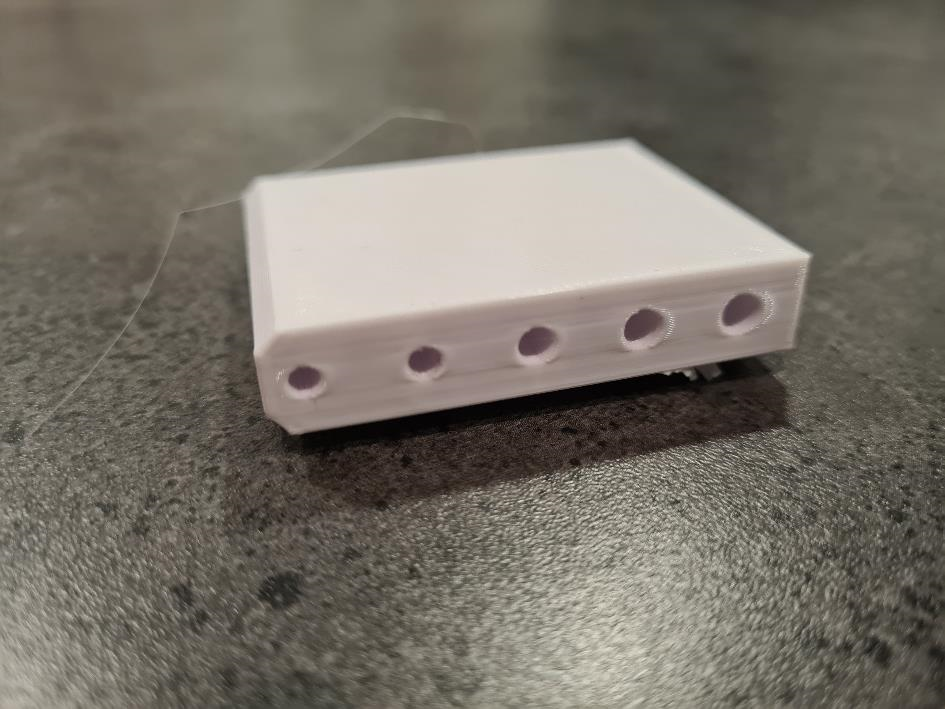
After I finished with the printing of the chess pieces, I have now started to print some of the parts for the arm. Earlier this week the nozzle on my printer got clogged, and I had to take some time to unclog the nozzle. Due to the printing of the arm not being finished when Wednesday came, I had made a prototype arm in plywood so that Kevin and Hossein could begin with the code intended for the arm.
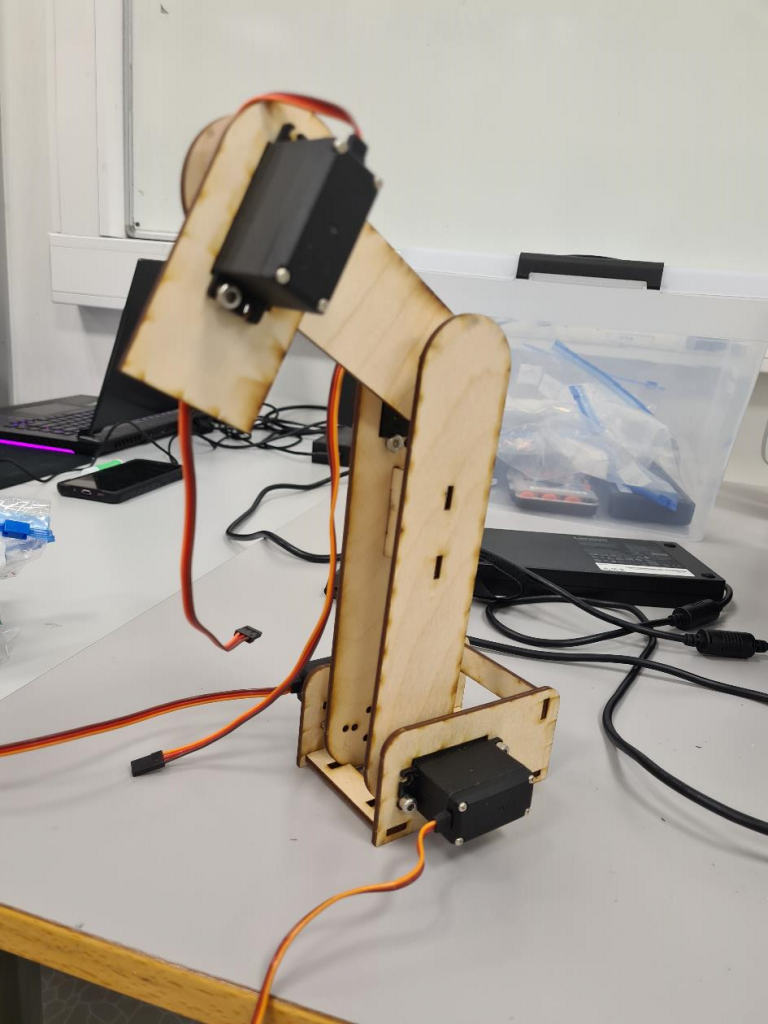
Workhours this week: 16 hours, excluding the print time.
Liv Marte Olsen – Mechanical engineering
Etter mer testing og mye som ikke fungerte med prototypen fant jeg ut at jeg må ha en egen strøm forsyner for motorene siden arduinobrettet ikke gir fra seg nok strøm til motorene. Fikk tak i ny strøm forsyner og tilhørende batterier og skal fortsette å kode prototype armen. (5 timer)
Kevin Johansen – Computer Engineer
Var med å hjelpe Kevin med å sette opp prototypen, men det ble en del feil her og der også med ledninge, strømforsyning, så mye tid gikk på dette
Hossein Sadeghi – Computer Engineer
Computer Vision
This week has only been used to annotate the last 265 images that’s left from my dataset. On Roboflow these is a tab that’s called “Health Check” which I have been monitoring the whole time through. This tab shows you an overview of all your classes, and if they are under- or overrepresented in the dataset. Since there are 8 pawns, 2 of each pair, and only one queen and one king in each colour I did know that all the pairs and the queens and kings would be underrepresented compared to the pawns. These modifications I will add next week.
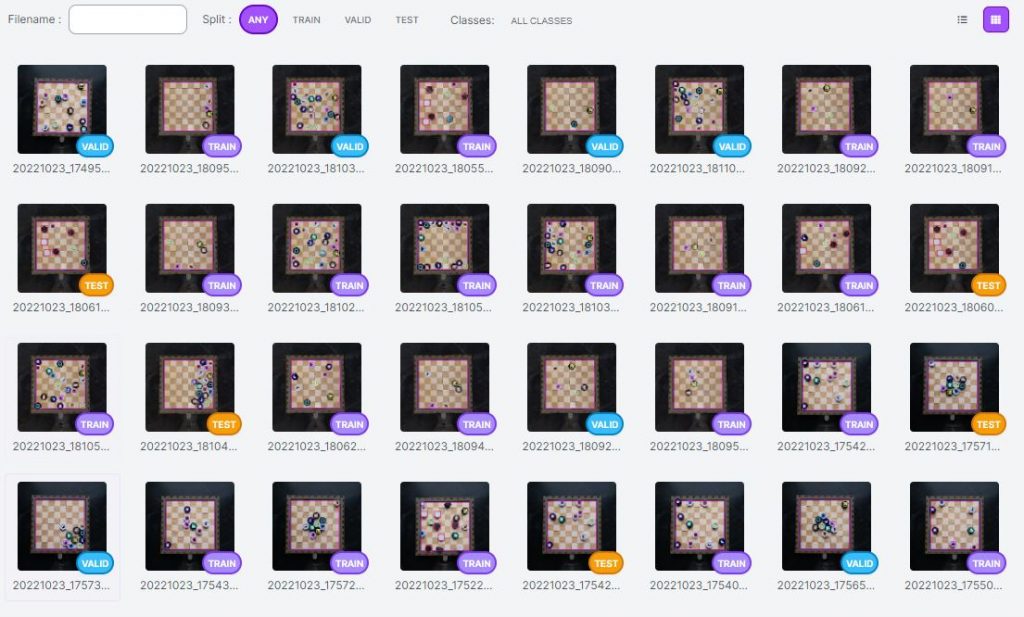
Hours on the project this week: 12
Marte Marheim, Computer Science