Started to discuss what we will do in the next weeks. We discussed if we could use the car that some of the computer students are using in another subject. This will save us a lot of time because we won’t need to do driving part from scratch. The car is complete, we just have to assemble it like an IKEA furniture. With the car we will get a body, wheels and motors to each wheel. If we decide to use the car and we see this will work, we will need to code the car in ADA language, and the arm in Arduino.
Adrian is then working further on getting a controller to work with the arm. He is now testing joystick. Adrian will also look into if we can use a wireless PlayStation 2 controller to control the arm.
Kristoffer and Senay looked into how everything will look like if we are using the car we want. The car without any of our arm on it is pretty tight and not more space for extra things on it, but we are trying to figure this out. We are probably just going to move some of the components around to get more space.
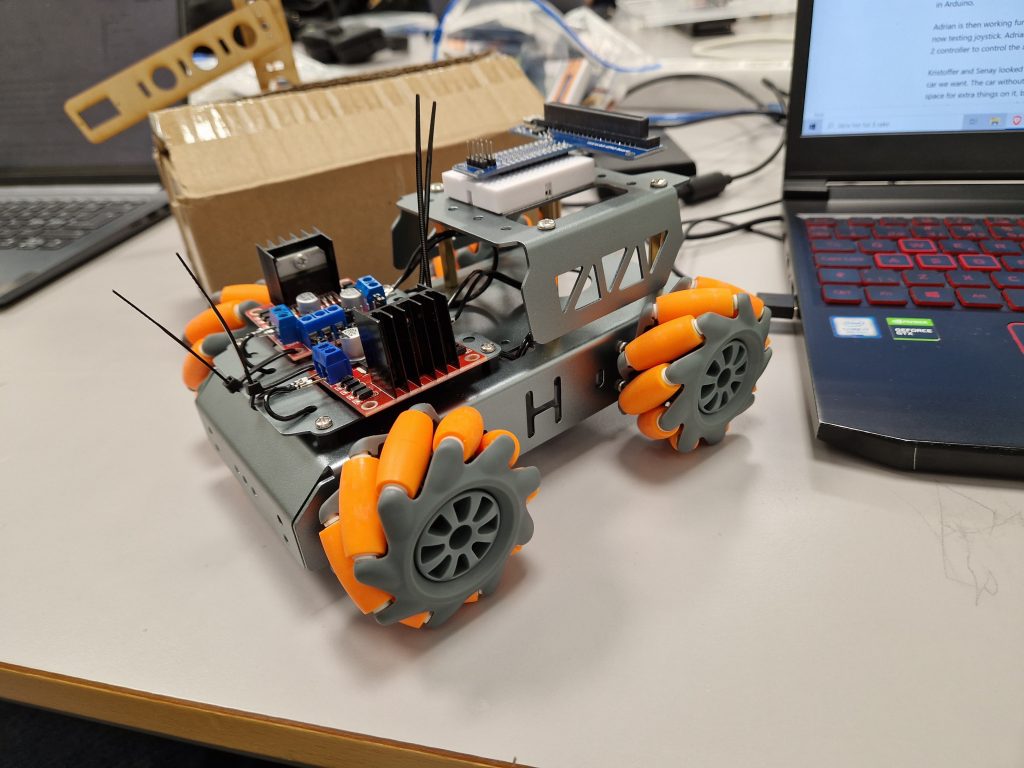
Sevag did some research on the internet trying to find some information or similar projects that have been done earlier to see how we can get the arm to smoothly rotate around.
Joakim tested the ability of the Arduino board according to how many servos one board could do. This is because we are going to use a fair amount of servos on the arm, so we need to be sure that all electrical components are able to handle that amount of servos. I think we at the moment are using 5-6 servos.
Dag is further working on the claw. When he tried to use the claw with a servo motor, he discovered a big problem with the claw. When powering it with a servo the claw doesn’t work like it should. The claw locks itself so the claw wont open and close itself like we want it to do. This results in that he needs to go back to the drawing table and change the design of it. He also made two different concept with bigger servo for the arm. One that was based on the first prototype and one that was more compact.
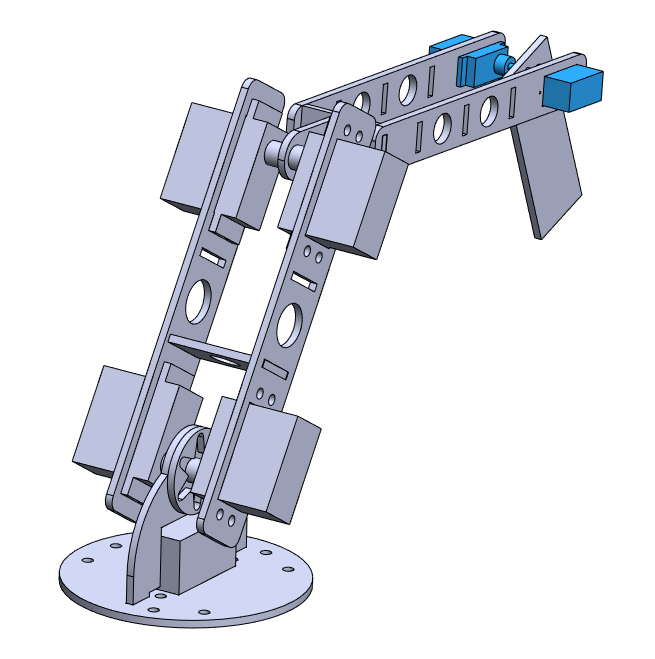
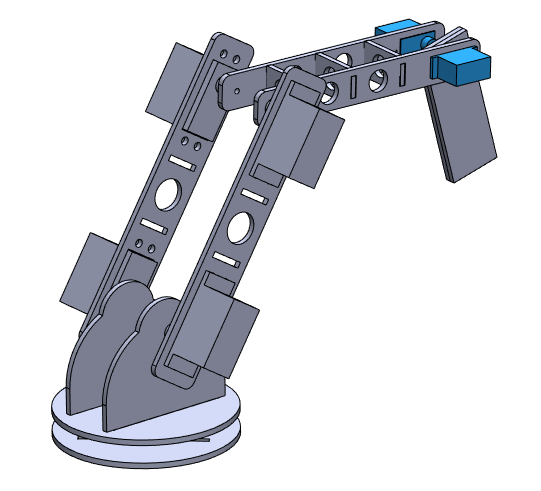
The new claw design.
This design is more compact and have a more direct connection to the arms. The benefit is that this design is simpler to produce and are hopefully not as prone to failure. What we hope to active is a design that will work not only one time but every time.
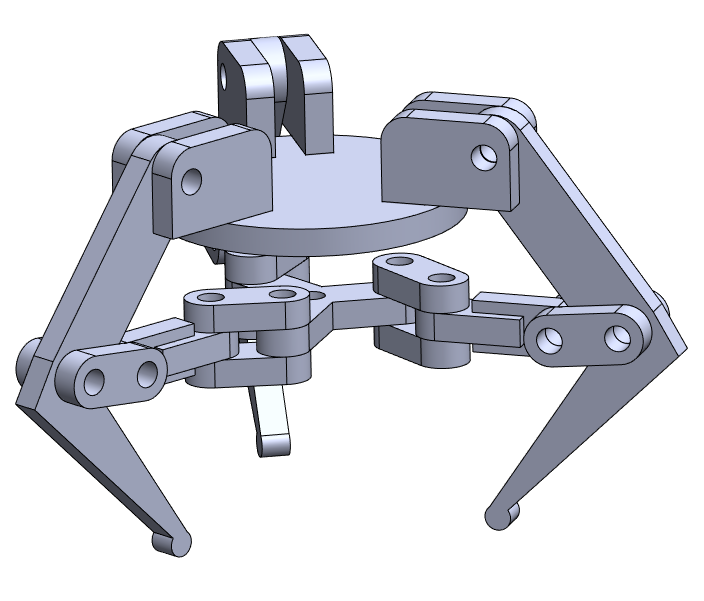
At the end of the day we got a message that we shall have a presentation next week about our progress etc. so we talked about the points in the message that we should go through in the presentation and prepared ourself a little bit for that.