Software (Marius):
I have had some health issues this week so i havn’t been able to work as much with the project as i’d initially hoped.
Watering multiple plants functionality:
First i added some more functionality to the system where i use an array to make the system able to water several plants. As of now, i have chosen to use an array where each entry in the array represents one plant. Since the vehicle will follow a predefined pattern the first entry in the array will be the first plant, and the last entry will be the last plants.

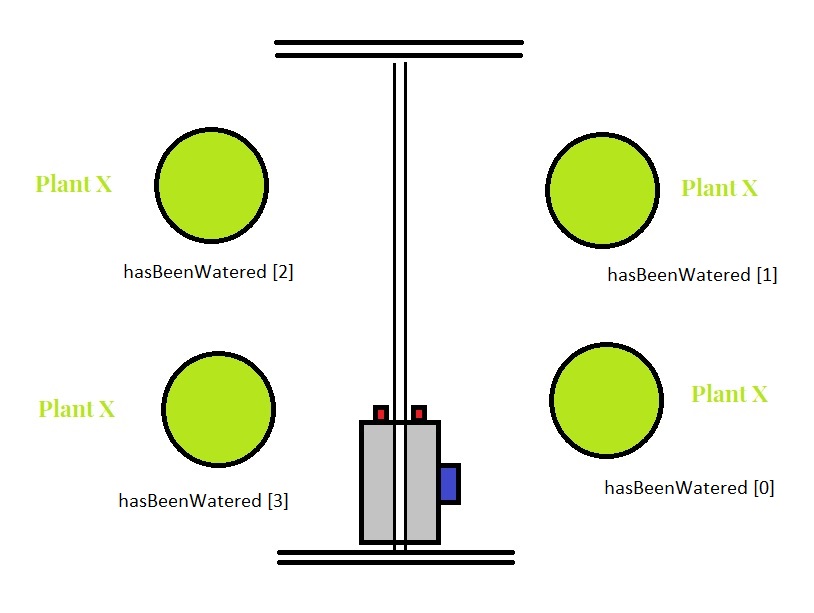
I looked into the idea of using RFID tags on each plant, but after doing some tests i figured out that this won’t work for our system. The distance between the plant and the vehicle will be to large so you won’t get any readings from the RFID. Plants can’t be placed any closer because the crane needs to have some space to be able to operate properly.
The system will now execute the following code for each plant in the array. I still have some minor work left as i need to make the vehicle turn right by 90 degrees right before the crane is rotated down, and also the vehicle have to turn left again after the crane has been rotated up. This will have to be done during testing.
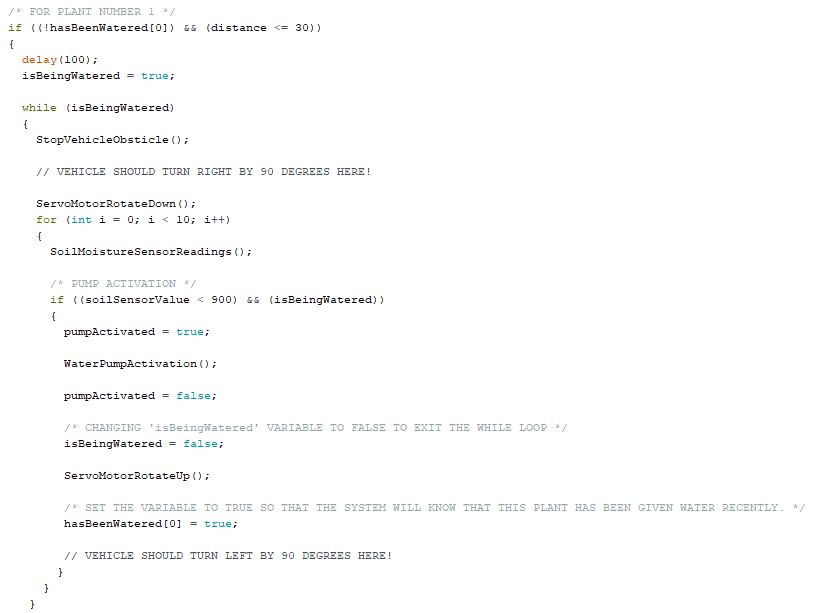
Mechanical (Shadi and Per-Terje):
We came up with an idea to remove the crane base and integrated it into the water tank lid cover to reduce the size of the chassis for the robot. Also, we start to print all the components again after a new iteration to fixed some small issues in design as we discovered during testing. the opening for the water tube on crane arm needed to be opened more and a radius was added to prevent the tube from bending. the screw hole for fastening the wheel to the motor riped open so we need to make new wheels with more area for fastening so it doesent rip apart as fast. the wheel spacers also need to be thinner so the drive weels can get better traction.
We faced a technical issue with our 3d printer with the nozzle, so we had to order new parts, and we send some of our designs to Riched to print them. He printed our battery box . And the metal pole endings on both sides of the box had to be bent and grined to be able into shape them to fit in their place.
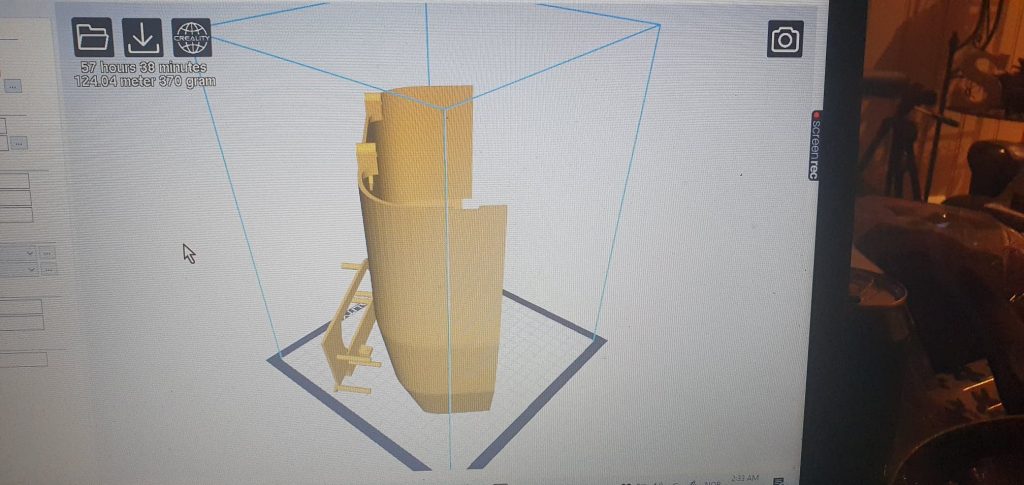
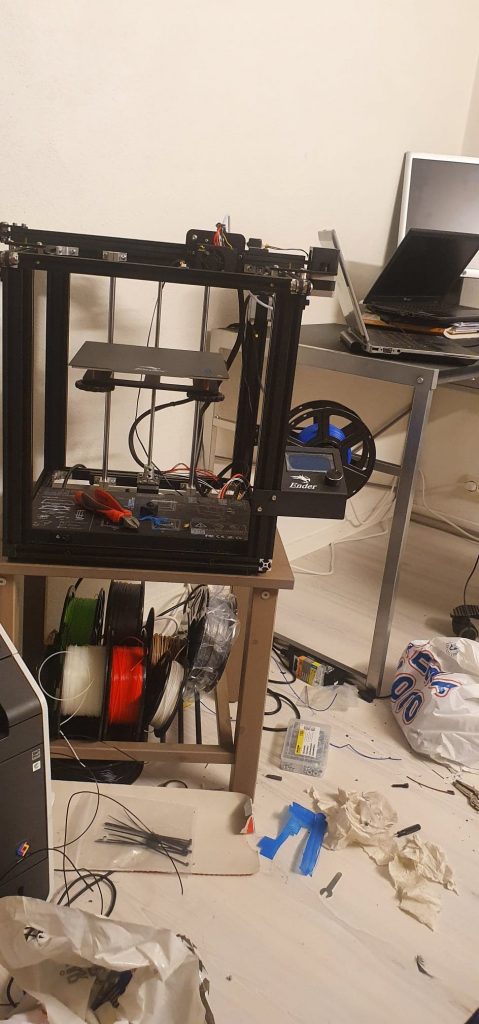
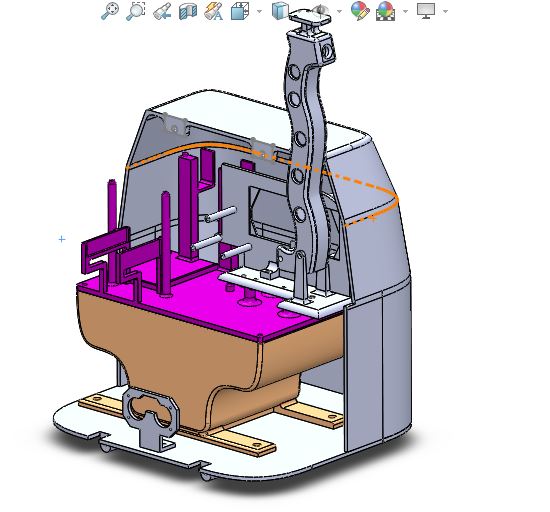
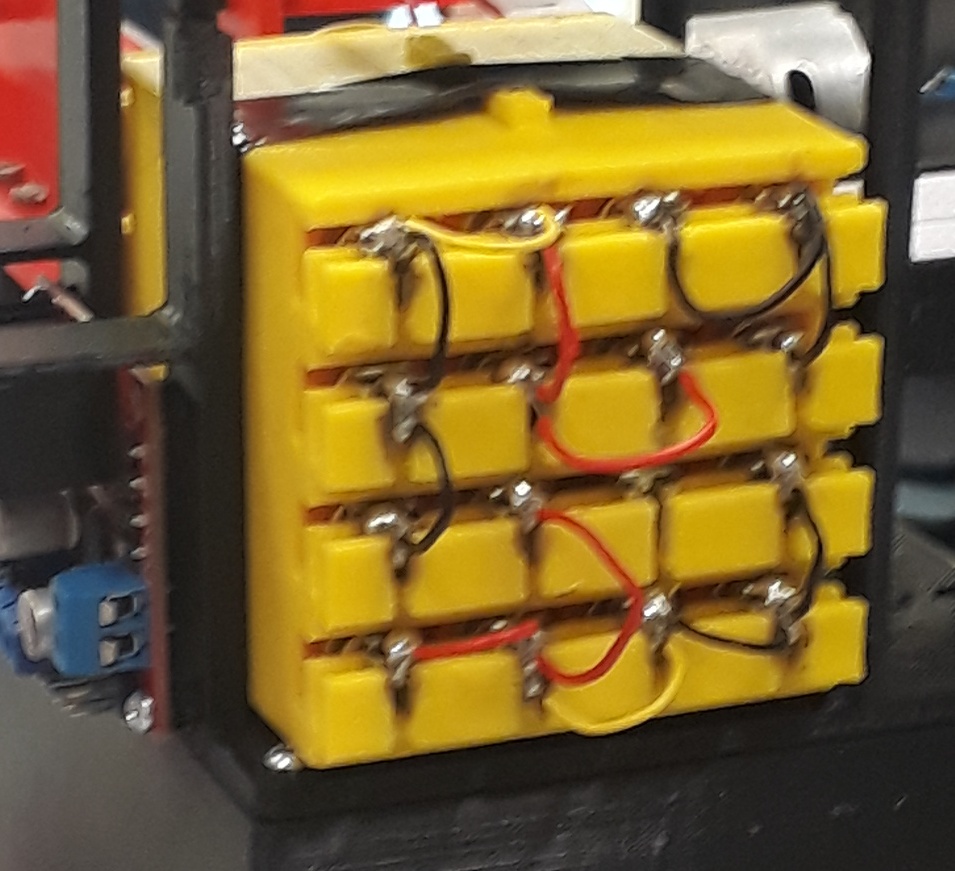
Electrical (Erlend):
Spent this week soldering together the battery holder for the 7.5 V and the 6 V.