Mechanical (Shadi and Per-Terje):
During this week we have been working on the design of the castor wheels brackets, the components bracket (which will be a stand for the arduino board, battery etc.) and the crane. The 3d-print of the parts was done on wednesday which meant we could attach some of the parts on our thursday’s group session.
We had some issues with 3d printing the parts where the crane arm had some defect because of using less than enough supporting material
The castor wheel brackets was almost a perfect fit, except that the holes did not fit with the holes in the plexiglas. After some minor drilling it was okey.
We did not have enough time to take any pictures of the components bracket and the crane attached to the vehicle as we focused on testing the line follower functions during this session, but we included some pictures of the parts on its own.
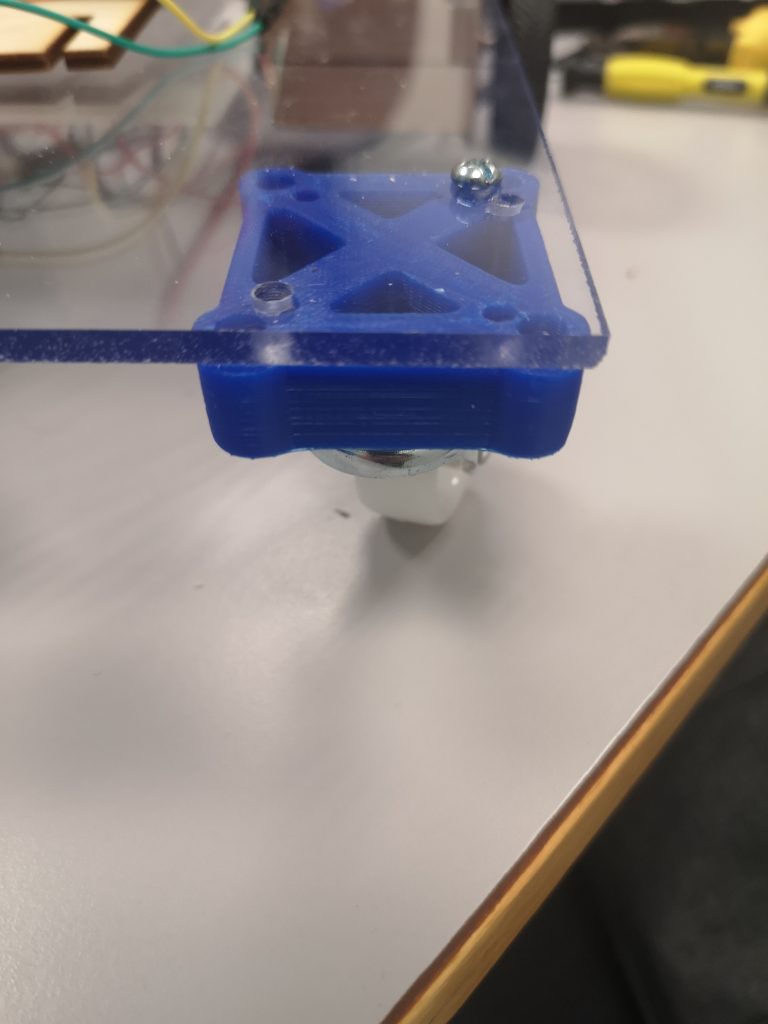
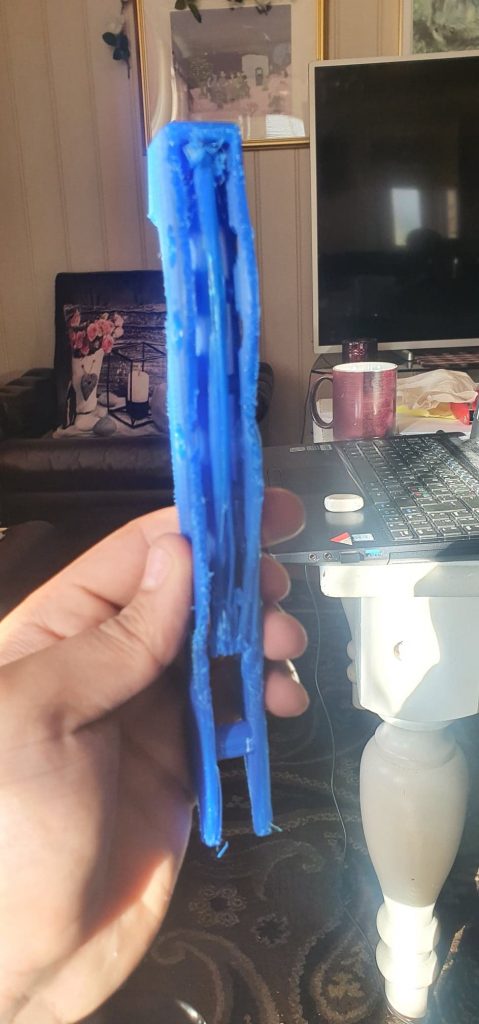
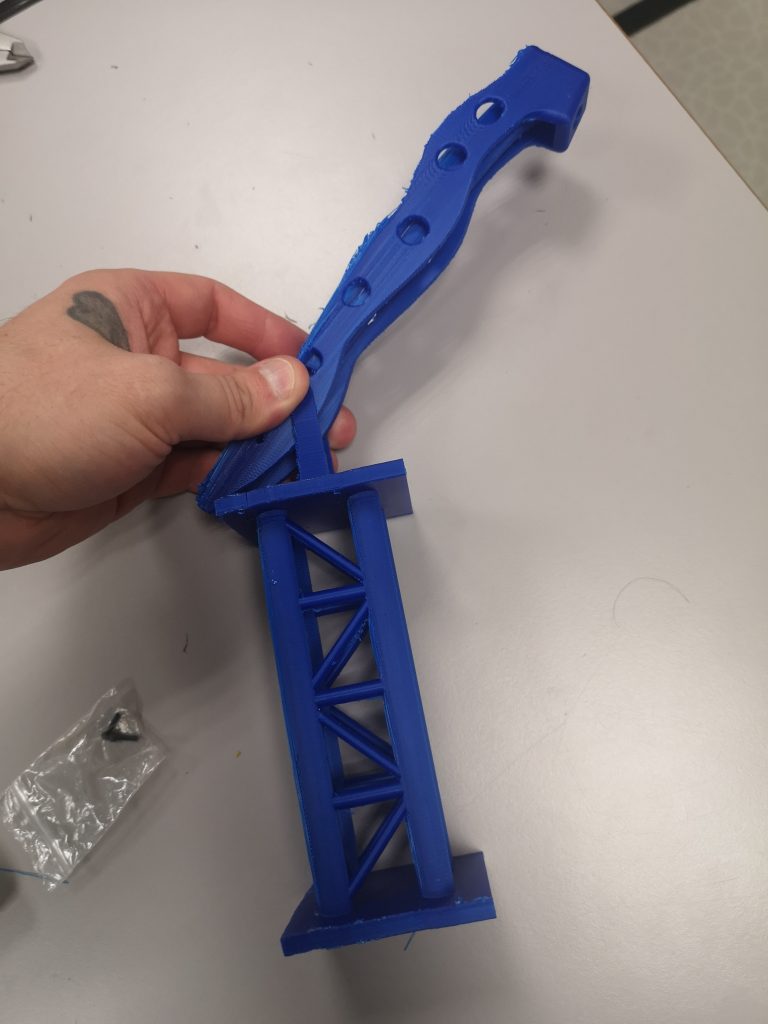
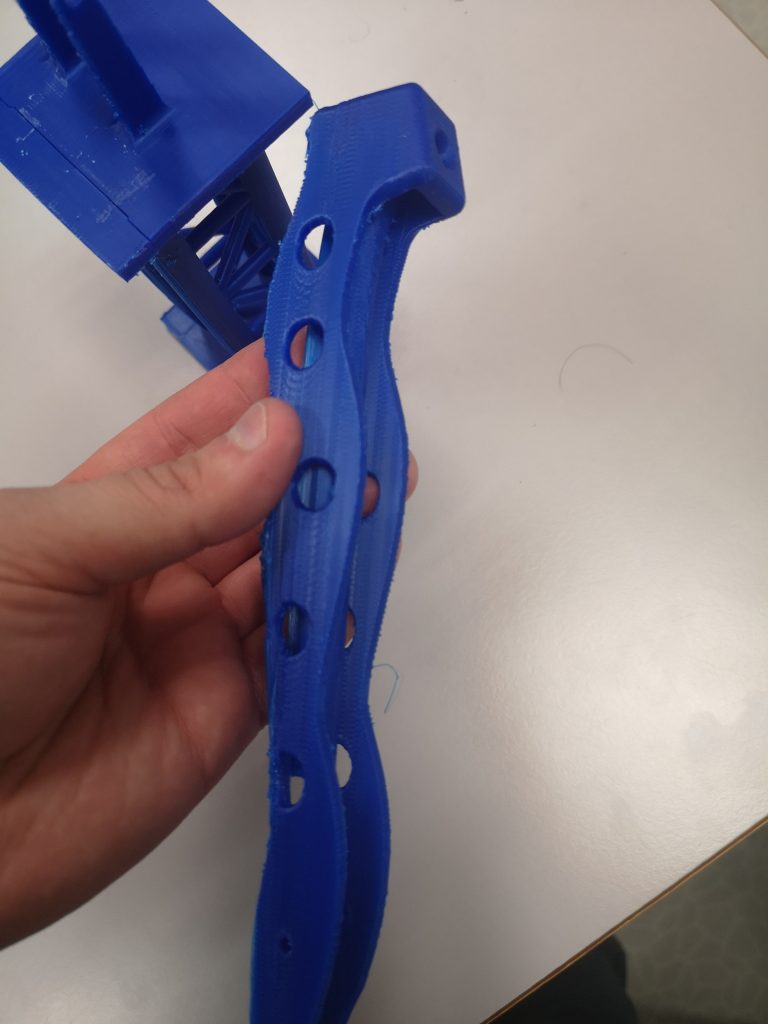
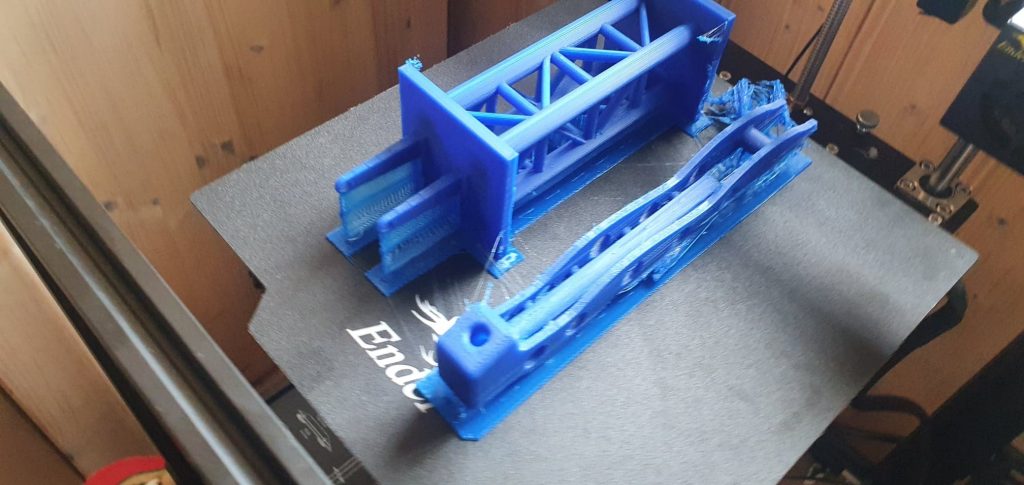
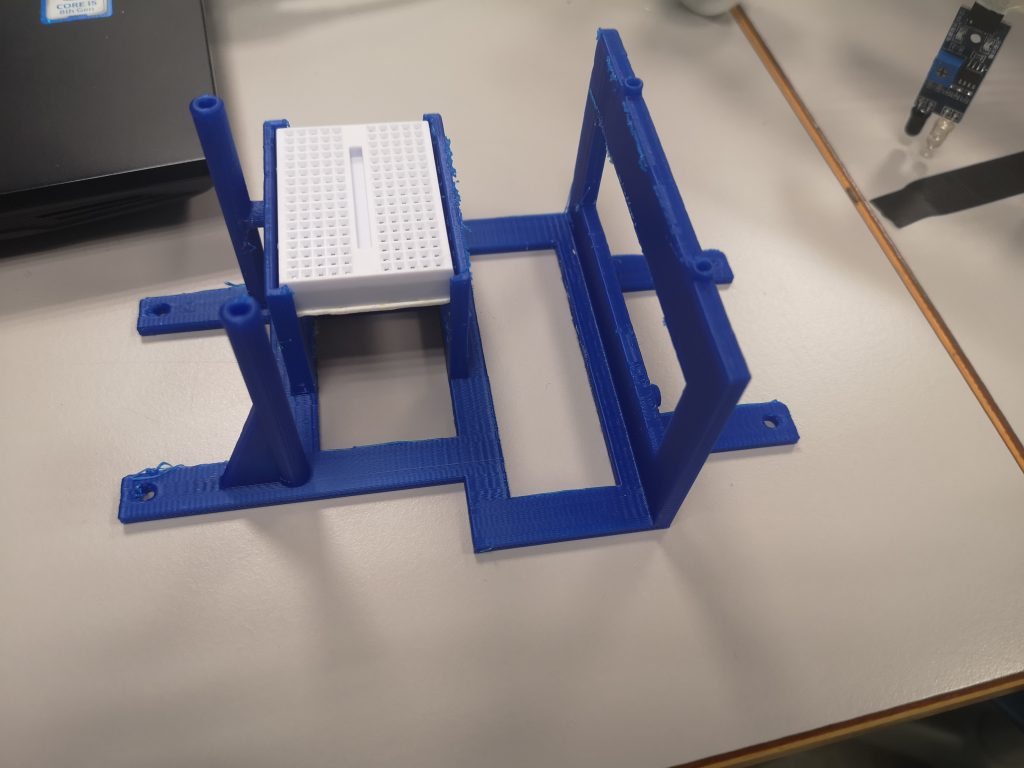
Software (Marius)
During the thursday session i have been working on the programming for the line follower sensors. The sensors we decided to use in our project is two IR transmitters and IR recievers which are used for sending and recieving light. When the IR rays hit a white surface it is reflected back to the sensor and generate some voltage change. When it hit a black surface the light is absorbed and no light is reflected back to the sensor.
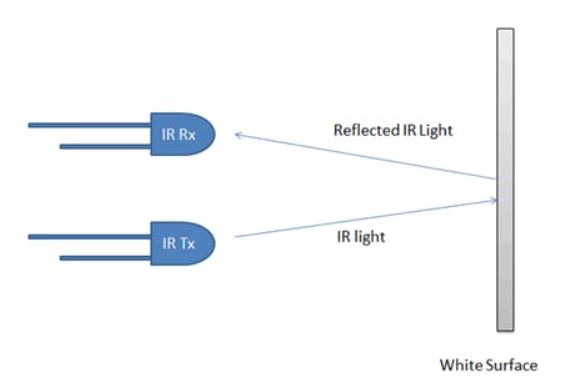

I had some minor difficulties getting the input from the IR sensors working properly. Normally, when light is hitting a white surface it should result in the input 1 on the Arduino, and when it hit a black surface it should result in the input 0 on the Arduino. I got some wierd values at first, but managed to get it working after a while. Since the Arduino will recieve 0 and 1 values it’s perfect to use some logical operaters in the programming.
After being done with the programming we did a few tests to make sure that the line follower sensors works as intended. I had to change the speed of the gear motors several times to make it go slow enough or it would just go straight into the walls.
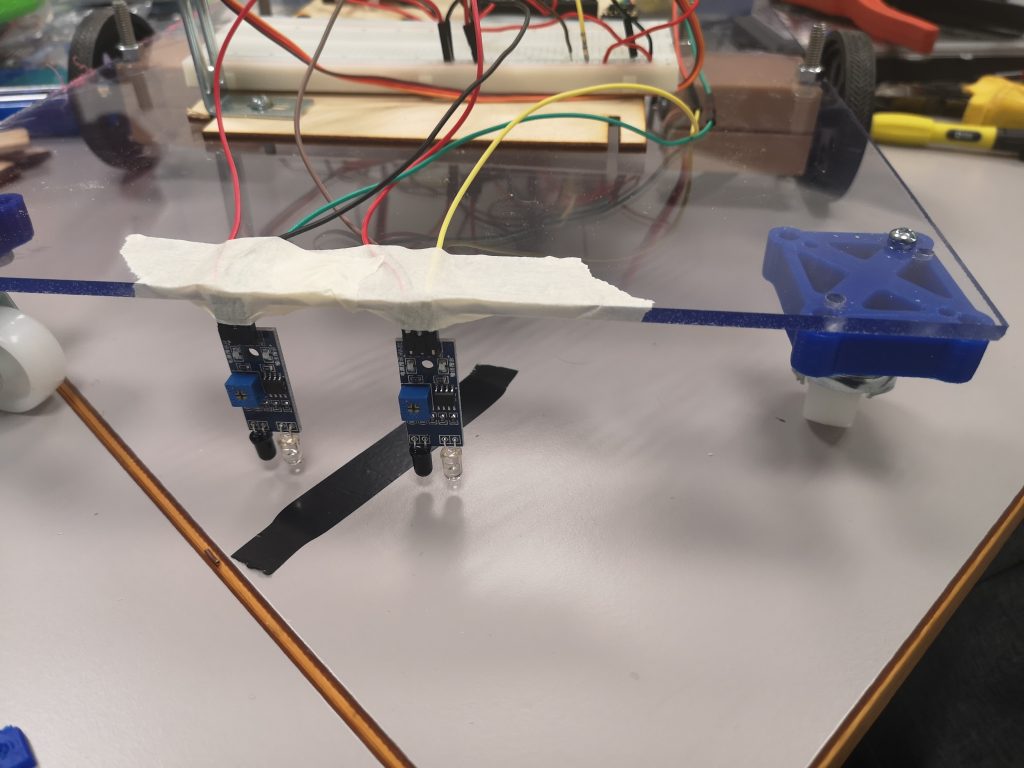
I forgot to take some screenshots when working on the software for the sensors, but i did remember to take a picture of our mess! 🙂
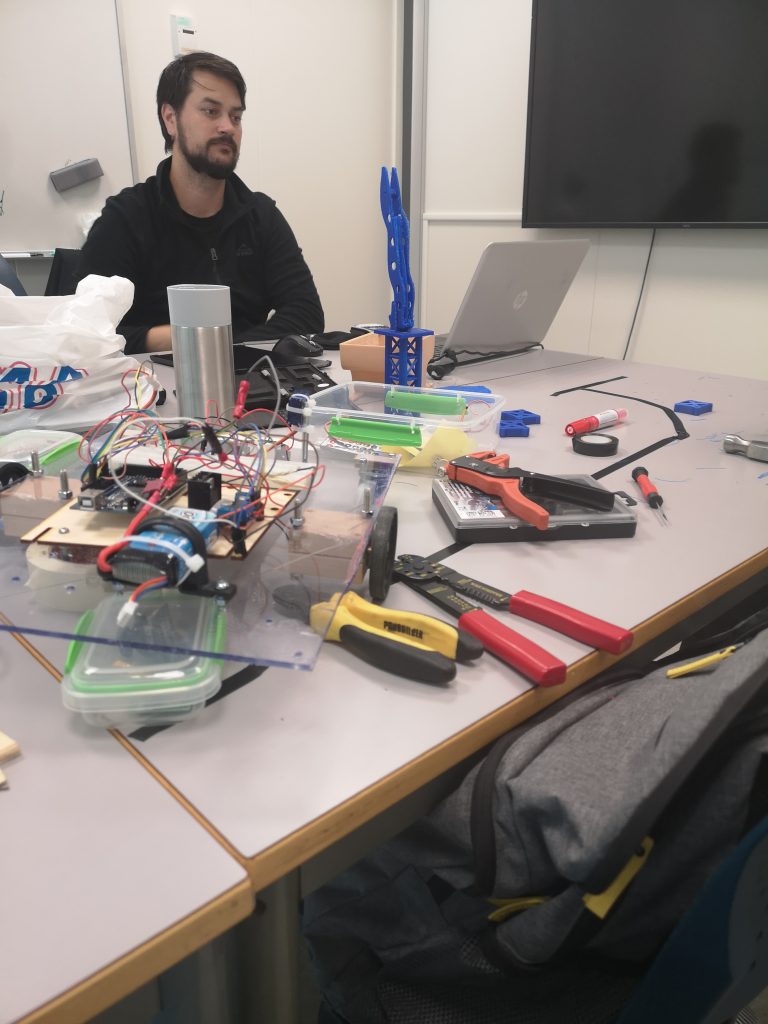
Added a video of our line follower testing: https://streamable.com/55sc4k
Electrical (Erlend):
Most of this week has been spent on research and testing, both regarding which servo motor is best suited for our use and which water pump would work for our design. Regarding the servo motor, the choice was between two different types, the SG90 or the bigger MG995. After some thorough testing and research, I landed on going forward with the MG995, which compared to the SG90 delivers a much higher load capacity and speed, the quality of the component itself is also much higher.
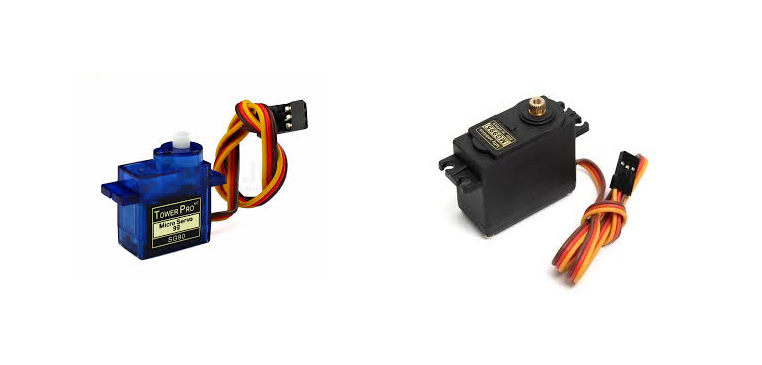
For the water pump I ended up going for a RS-360SH which was acquired from dronesonen. Seeing as this pump is more than capable of delivers the required amount of water needed, and that the size and weight of the pump is relatively small/low.
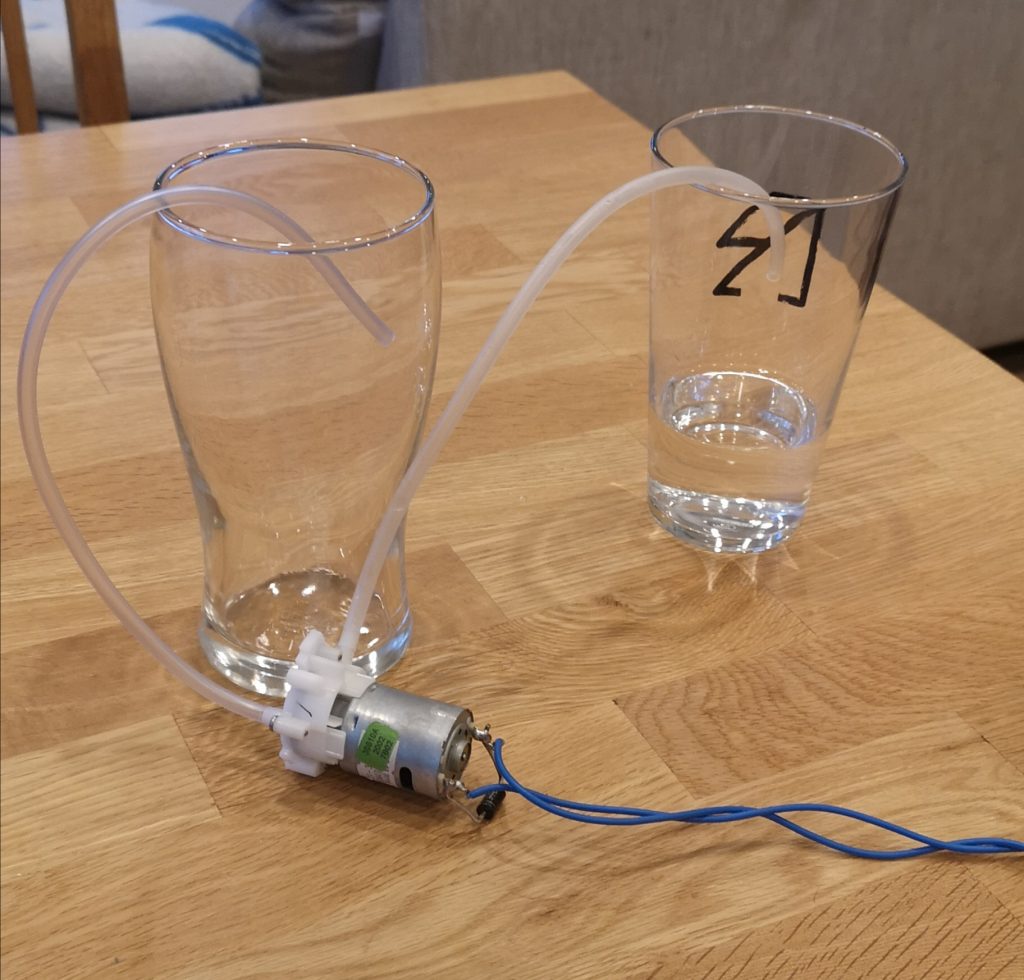