This week we finally got the lidar for the positioning of the trolley, but after some discussion with Steven, we ended up with the first idea we had, counting steps. The stepper motor is so accurate, and since the gear mounted on the motor fits perfectly with the power delivery belt, the easiest solution is using steps for this.
We tested the motor to see if it was strong enough to pull the trolley. The motor is strong enough, and we found max speed to be 175 rpm.
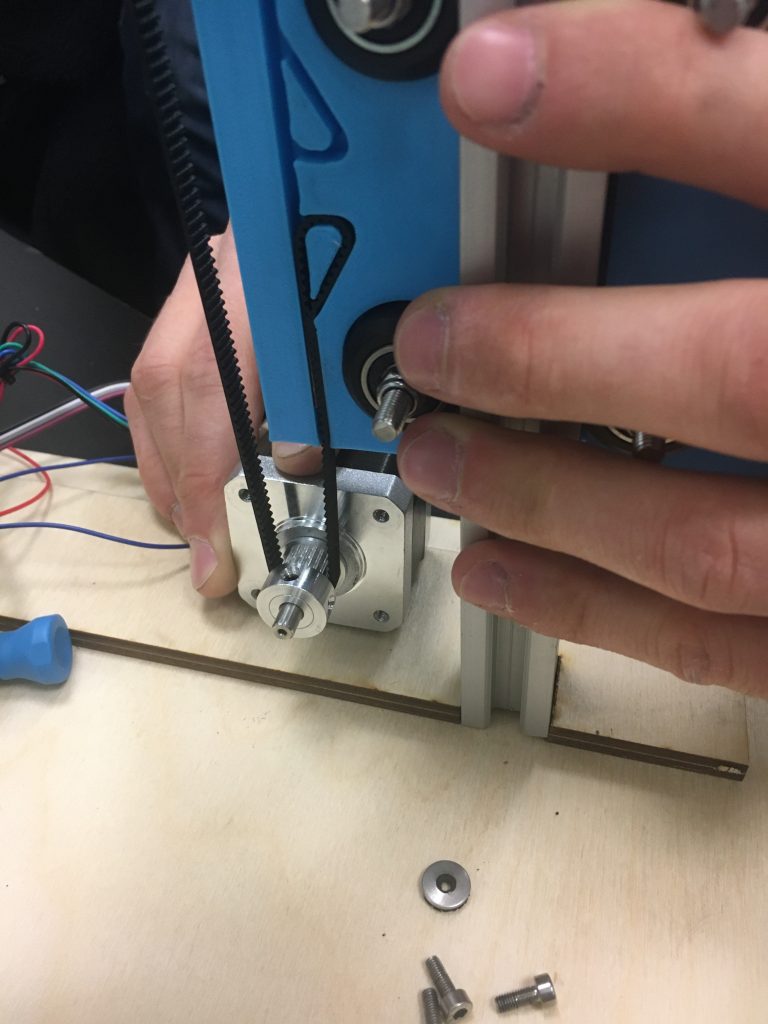
.
We have 3d modelled the holders for all six pumps, now we have to think of a way to mount them into the system.
The rest of the parts needed for the construction are finished printed, and the other stuff like walls and tubes are finished painted.
For the 3d scanning of the volume we finally got the ultrasonic sensors we needed, and we now have two alternatives. One movable and one static.
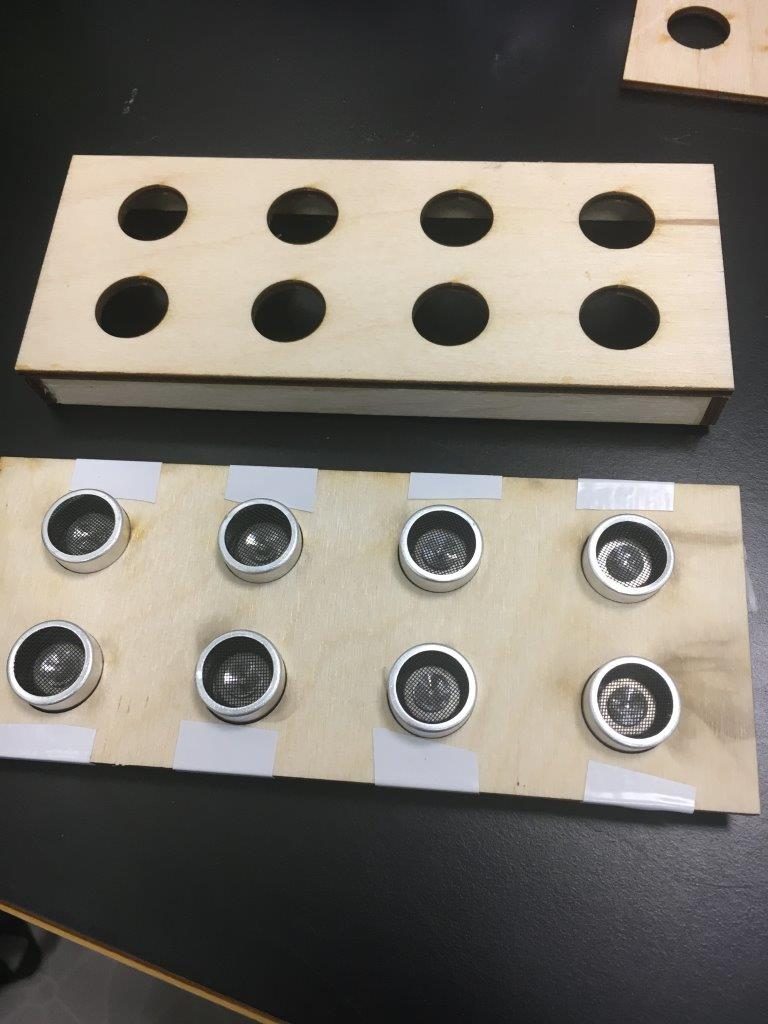
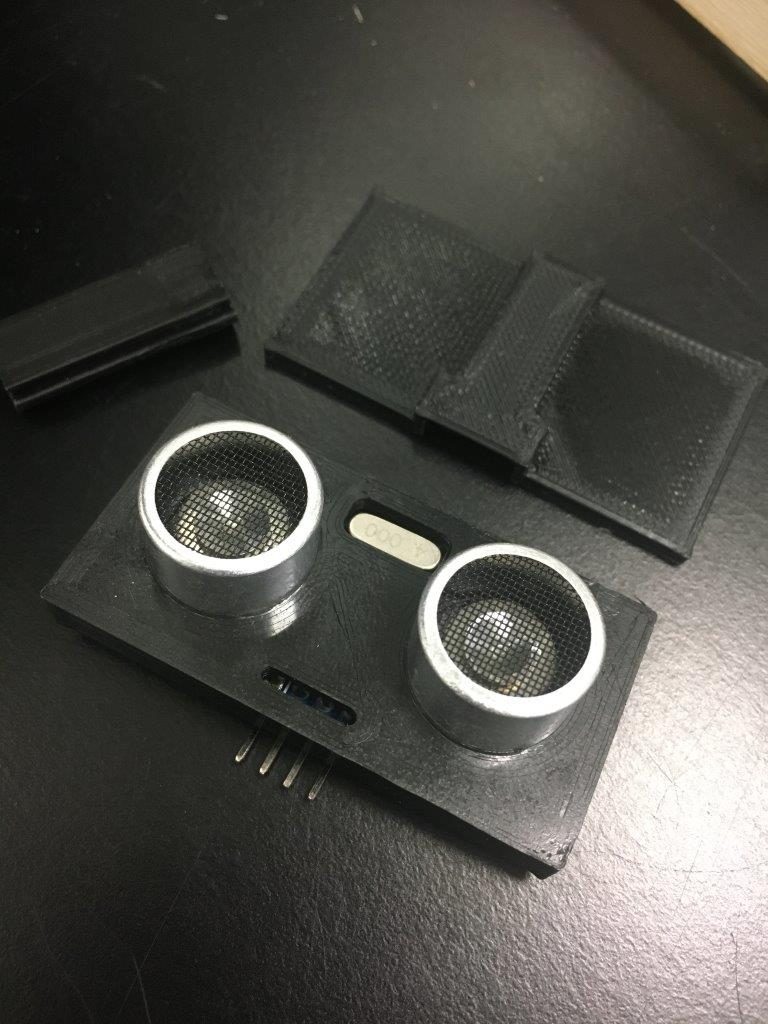
For now we think the static system is working better and the one we will choose.