Adam:
This week I was mostly a helping hand for Jacob and assisted him in most of the assembly, like putting parts together, drilling, crewing and advisor in terms of how to proceed next. We have also met with multiple teacher that were a big help to our work.
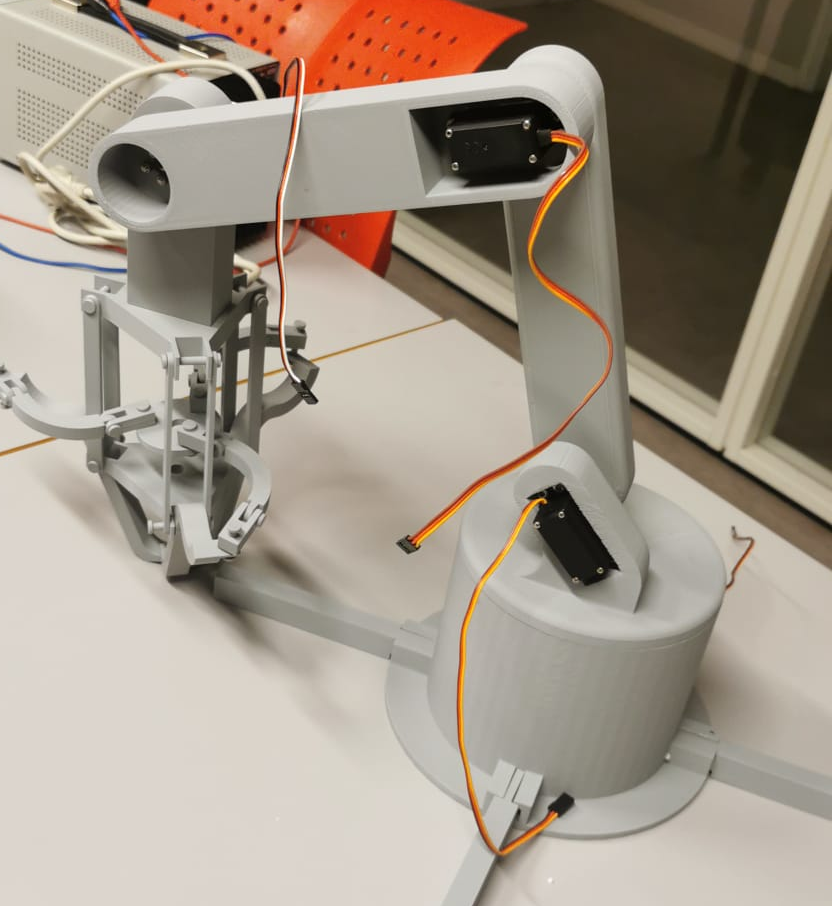
Adrian:
Now that the arm is assembled, I worked to test each joint and servo motor to make sure the arm can move as intended. At the end of the week and on the weekend, I’ve given the arm to test it’s strength and moveability. Some servo motors had to be replaced. Others weren’t the correct version. However, even with all the right servo motors, with the power Arduino gives out, it wasn’t enough to power all of them at once. Then, with an external power supply, it still had difficulties even with the max voltage I dare to give, which was 7.2 volts. At the end of the week, I gave the assembly to Farah to continue simulating and looking into integrating image recognition.
Jacob:
This week I took charge of the assembly. I first I put together the new reprinted model, then when I found out we didn’t get screws. After we got screws we found it the holes were too tight or they were not there at all. So I took the assembly to the machine shop and drilled some bigger and more precise holes. Then with help from Adam I screwed in the claps for servomotors. When I was screwing in the motors and immediately testing them, we found out out that some could have been damaged or not working properly. We met with almost every teacher in the school this week to help us with variety of things, but ultimately I was able to put the assembly together and gave it to Adrian and Farah for further testing.
Pamela:
This week Sergi and I tried to do the FEM analysis in the most critical position, which is when the robot is in a completely horizontal position and tries to pick up a certain weight.
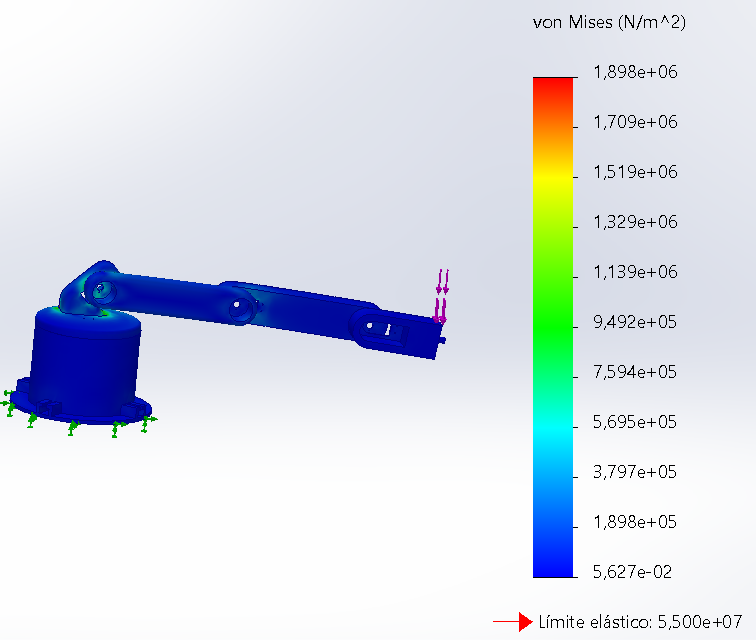
However, we noticed that the robot hardly suffers from the force of the weight of the bottles it has to pick up.
Sergi:
During this week, I started the FEM analysis of our robot with Pamela’s help. We had to fix the hole base and we put a force of 0,2N because we are lifitng 12 grams plastic bottles (medium size). With all these conditions and putting the robot in the maximum stress position (totally horizontal), because this way the momentum (torque) is the highest as the distance to the base is larger. The most problematic points are the joins between the arms, specially the join between the first and second arm, where is the most critical point.
The photos are in Pamela’s part.
I also contributed on the assembly of the robot, since we met to assembly it together. Here there is a photo of how it was going during the assembly process:

At the end of the week. I finally managed to do the right FEM analysis thanks to the advices of Richard. He told us to do the FEM analysis on some pieces separately. So first I did the arm 2 individually and I analysed as Richard told us. Here are the images of the result:
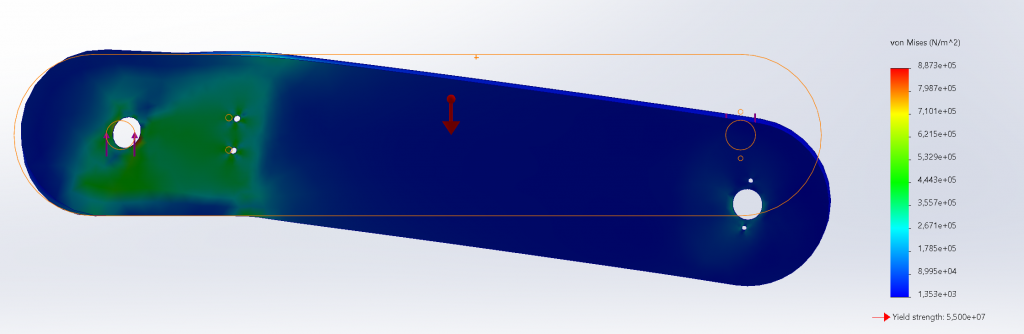
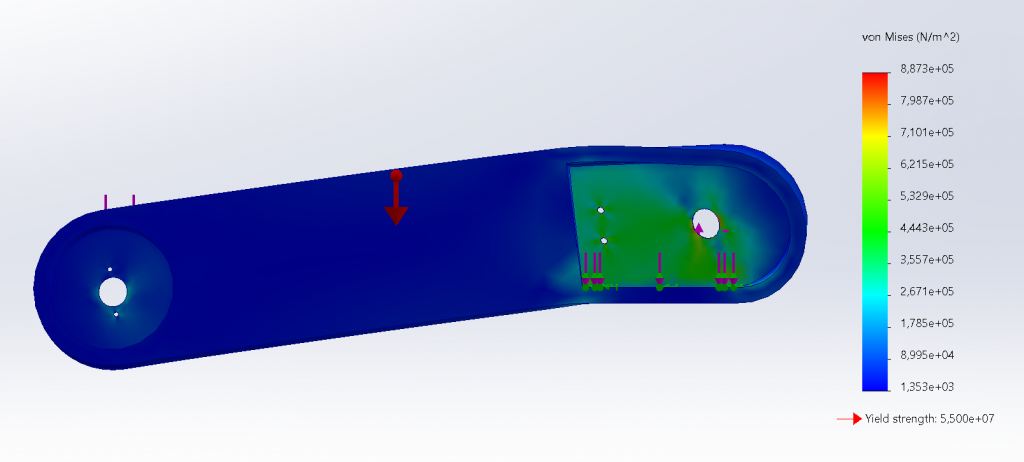