Shanel:
This week, I finally saw my parts in action on the real-life prototype. With all the parts for the vertical design printed and working, I can now start planning out the horizontal layout. It’s exciting to see things coming together!
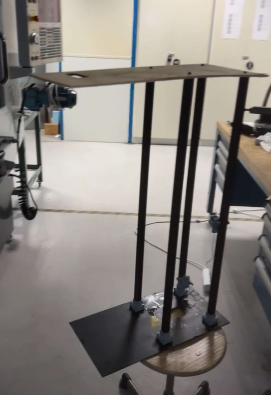
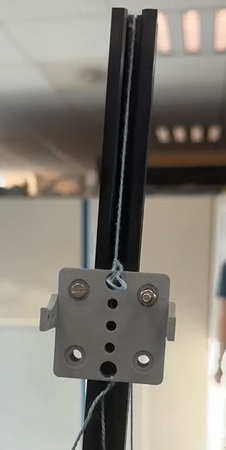
Now that I have the vertical parts for movement ready, I am gonna work further on to work on the horizontal parts and design.
Azi:
Making the Elevator Simulation
This week, I had to take the elevator system code we already had and turn it into a proper simulation. Because all of the physical elevator isn’t ready yet, and we still needed to show something for proof of concept, and test the system. So, instead of the hardware, I got everything working virtually to demonstrate how the system would actually run.
What I Did
I started by tweaking the original code, which was made for the real elevator setup. I adapted it so the platform movements could run virtually instead. That means I programmed the horizontal and vertical movements to work in a simulated way, but it still follows the same logic the real elevator will use.
Next, I hooked up the database to the simulation. Now, when a car gets parked, it marks the spot as “occupied,” and when it’s retrieved, the spot goes back to “available.” Everything updates in real-time, so it looks and works just like the real thing.
How It All Works
The whole setup ties together the movements, the database, and the interface. When you park a car in the simulation, you’ll see the platform move, the parking spot status update, and the system issue a receipt. When you retrieve a car, it does the same in reverse—moves the platform, updates the spot, and resets everything.
Demonstration
To explain all this, I made a two videos:
- One shows how a car gets parked. The platform moves, the database updates, and the spot turns red in the interface to show it’s taken.
- The other one shows the retrieval process—getting the car back, the spot turning green, and the platform resetting.
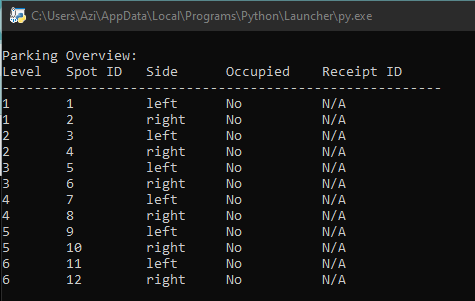
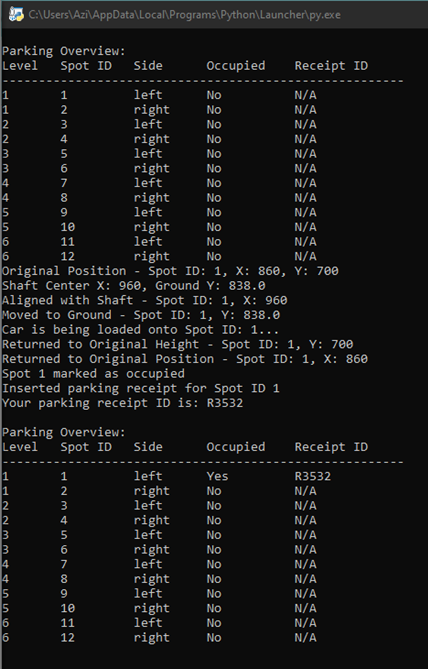
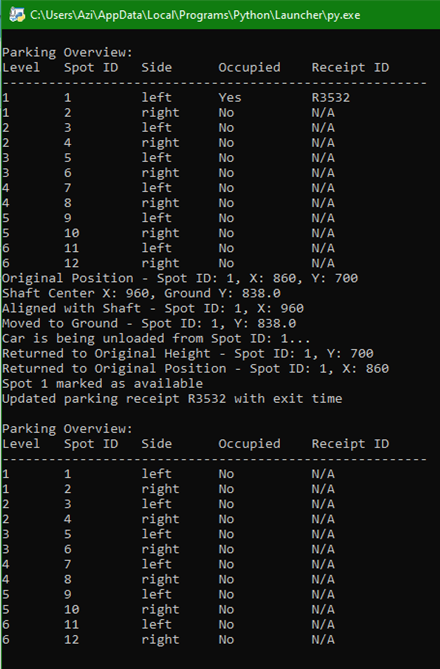
What We Have Now
The simulation works perfectly and shows exactly how the real elevator system will run. Even though the physical setup isn’t ready yet, this simulation is a solid stand-in and makes it easy to see how the system handles parking and retrieval from start to finish.
Milani:
I restarted the Python project called “Screen” using Flask. The initial implementation was done with VMware, but I noticed that the mouse pointer was still visible, which interfered with the functionality since I wanted it to be entirely touch-based. As a result, I decided to start from scratch to ensure a better touch experience.
- Created the main structure for the Flask application without using VMware.
- Defined routes for the main menu and start screen.
- Developed basic CSS styling for a responsive and touch-optimized design.
Challenges:
The main challenge was discarding the first attempt and starting over to achieve full touch functionality, but it was necessary to ensure optimal user interaction.
Benjamin:
This week has mostly gone in to fixing small errors and details on the website. I added a little header, just because it looks a bit more professional. Some of the buttons were bugging out a little, and by this i mean redirecting you slightly wrong when you press it. The functionality was there, but it just wasnt a good user experiance. So figuring out the issue there took up quite a bit of my time. Some of the border settings were messing with the button functionality, but all fixed now!
Meron:
Workshop and Design Progress: Elevator Base and Building Design
This week, I made significant progress both in the workshop and in the design phase of the smart parking project. In the workshop, I focused on key tasks related to the elevator system. I started by precisely measuring and drilling holes in the metal plate that will serve as the foundation for the elevator. For durability, I chose a strong metallic material capable of handling heavy weight during operation.
Additionally, I worked on assembling the elevator profiles (metal rods) and connecting the entire lift system. Using a sawing machine, I cut a plate for the elevator platform, opting for wood to make it lighter and reduce the strain on the motor during lifting operations.
After completing the assembly, I could see the entire elevator system prototype functioning as a cohesive unit. This was a crucial milestone, providing a clearer understanding of how the components interact. Additionally, I have been working on monitoring and connecting the entire system to ensure all parts operate seamlessly together.
In addition to the workshop tasks, I continued working on the building design using SolidWorks. This involved refining the overall structure to integrate seamlessly with the smart parking system. The design process has been instrumental in ensuring that all components align both structurally and functionally.
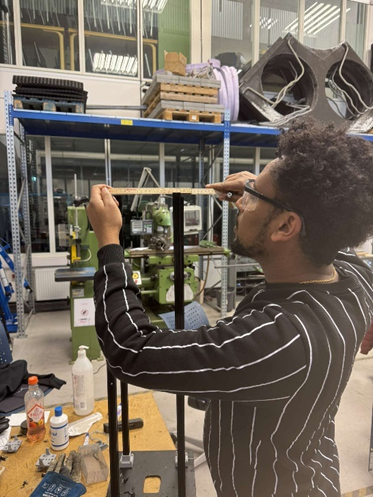
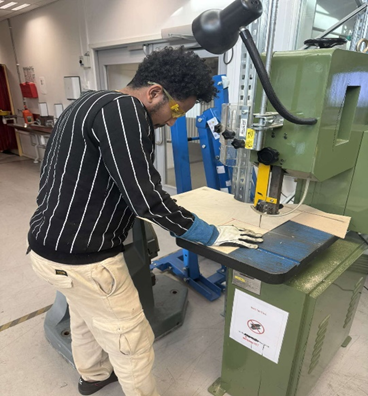