The seventh week was not a whole lot eventful, since there were slight hickups in our communication and attendance, since a lot of us were out of town or otherwise preoccupied.
Individual work:
Adam:
This week I haven’t done much only few improvements on the design of the jaws and doing some other stuff while waiting for the rest of the 3D model to be completed and sent to Richard for 3D print.
Adrian:
With the oral presentation done, my focus returns back to ROS, MoveIt and the URDF file. To properly put the computer engineers to work, myself included, I need to have the file done as fast as possible after the 3D model is finished. So what I’m doing this week is making a mock file with the information I already have.
Jacob:
I helped Adam with the 3D desing of the claw, helped with it’s movement restraints, designing interfaces, and generaly helping with the “big picture” of the whole arm itself. I also made some calculations to predetermine what kind of motors we need, and together with the mechanical group we went to retrieve them from Steven.
Farah:
In the week that followed, I put my ROS2 research to use and began setting up the simulation environment in Unity. This meant experimenting with basic robotic arm movements and seeing how ROS2 and Unity can work together for real-time simulations. This work was crucial in fine-tuning our future sprint tasks and shaping our development strategy
Pamela:
I improved the base of the robot as it follows, this is the definitive one for the moment:
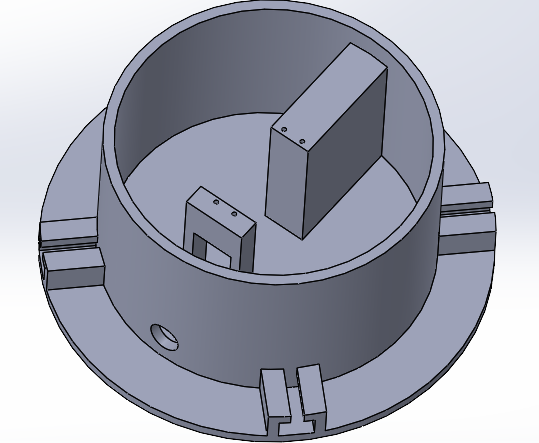
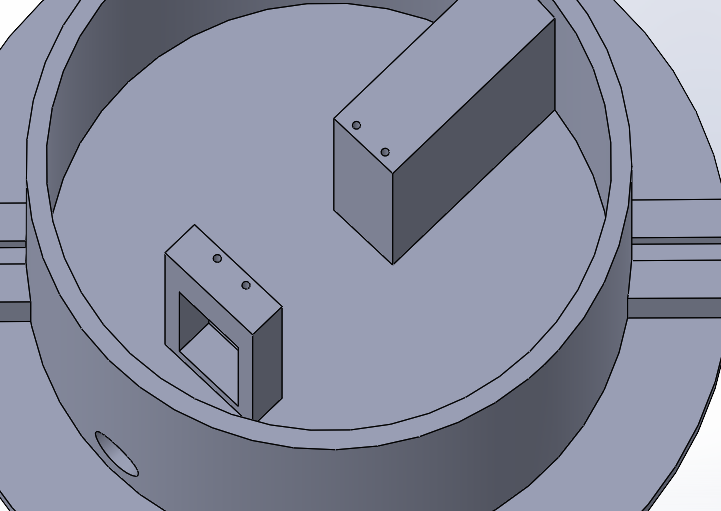
I made the legs for the base to gain stability and I also helped Sergi calculate the moments to choose the right motors.
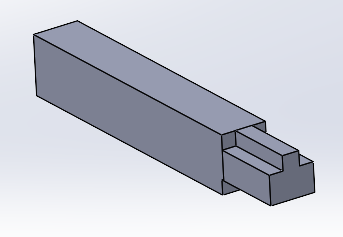
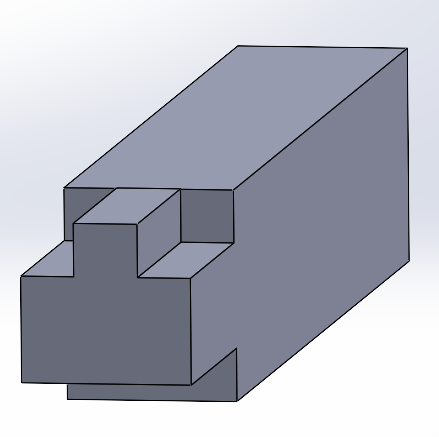
Sergi:
First of all in this week I looked at the servomotors that we would need for the base and for the arms. After looking the ones that university have and some calculations that I did of the amount of weight that they need to suport I arrived at the cocnlusion that we will use the Parallax Inc 4 servomotor (continuous rotation) for the base rotation and the MG996R for the arms (180 degrees):
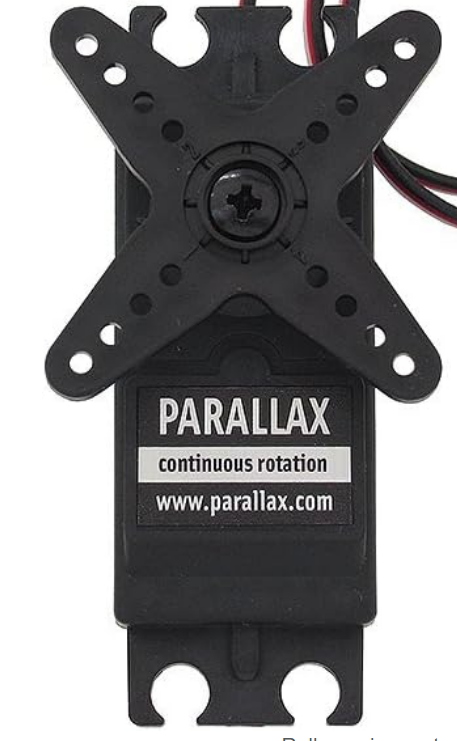
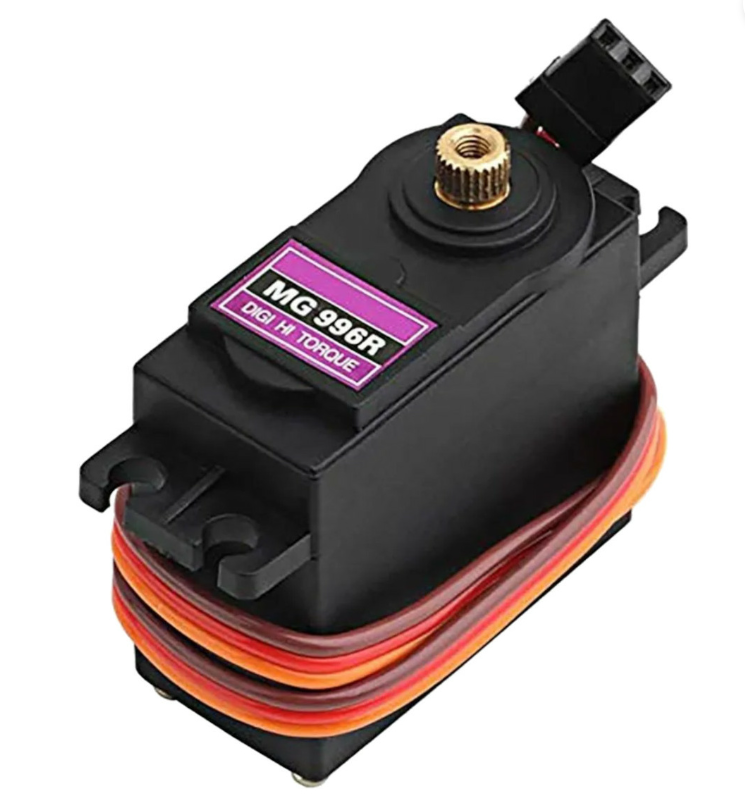
I looked at this website to see the measurments of these servomotors and be able to do the proper design in SolidWorks:
Continuous rotation: Amazon.com: PARALLAX Continuous Rotation Servo – 900-00008 : Toys & Games
Standard rotation: MG996R Datasheet | DigiKey
Here are the calculations of the momentum that each servomotor has to be able to handle in the position of maximum momentum, where the whole arm is stretched. This way we can know which servomotors we need.
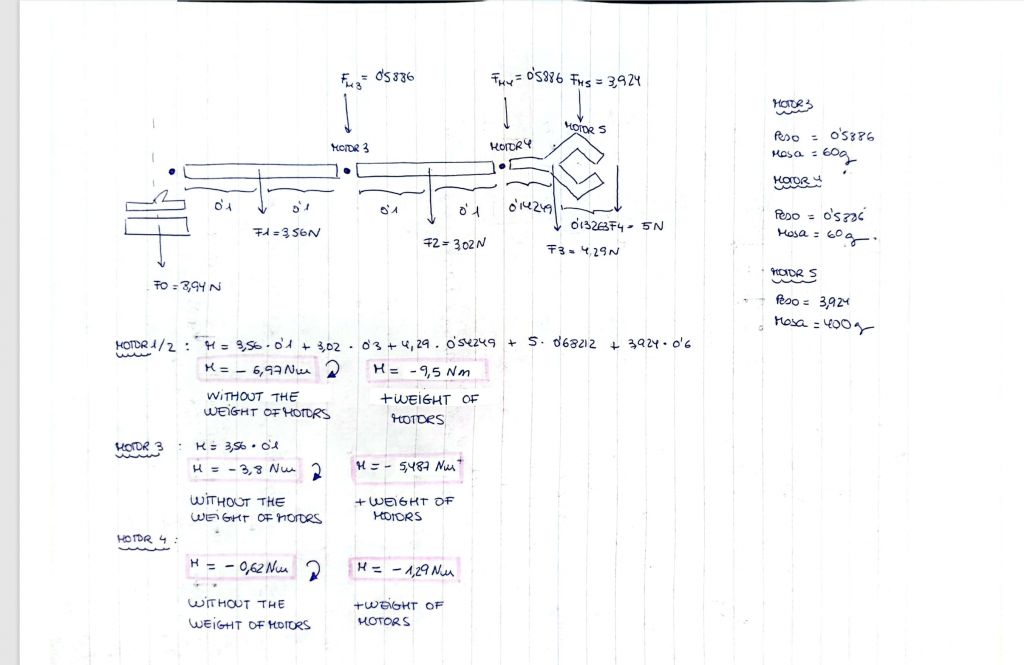
During this week I also improved the piece that goes on top of the base and connects with the first robotic arm. I adapt it in a way were the servomotor fits perfectly inside the hole of this design and we will just have to put some screws on that to make the servomotor fixed.
I also did 2 holes on the flat part to screw it with the servomotor that will go under this part (continuous rotation base motor) and will make rotate the whole arm in reference to the vertical axis:
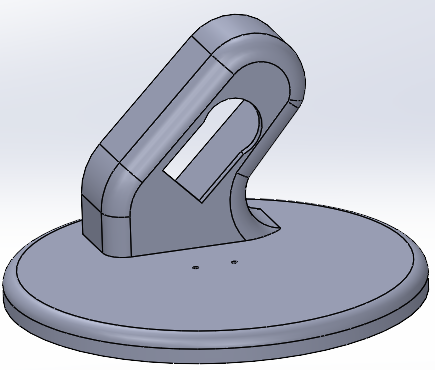
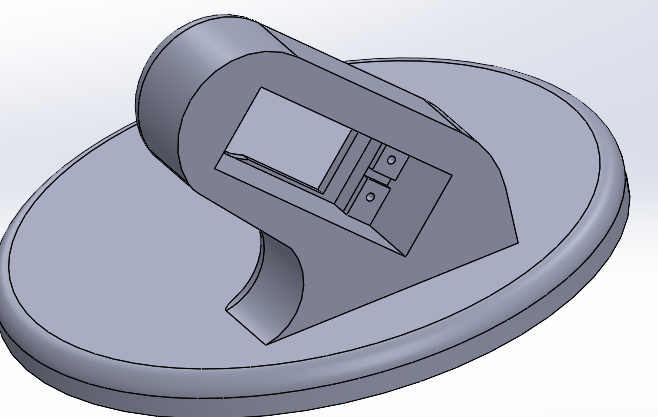
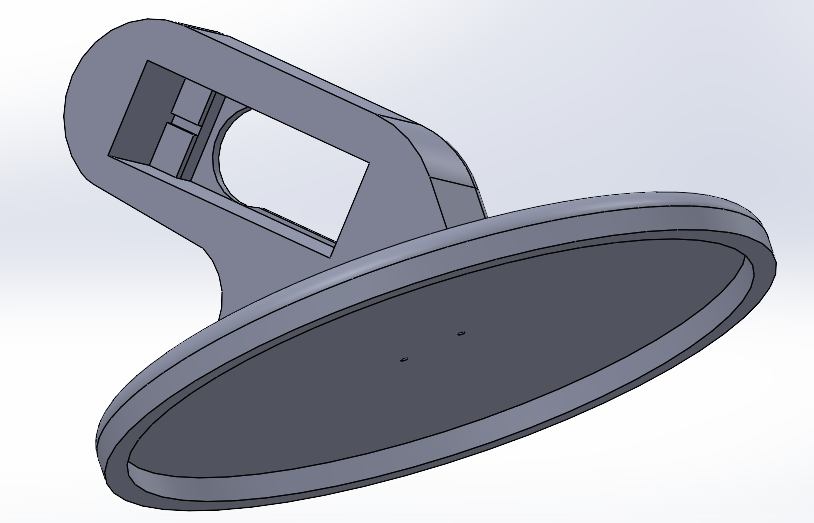