Andreas
This week has been good as our prototype is practically ready to assemble. As for what has been done this week, there has mostly been testing designed electrical components to ensure stability and reliability.
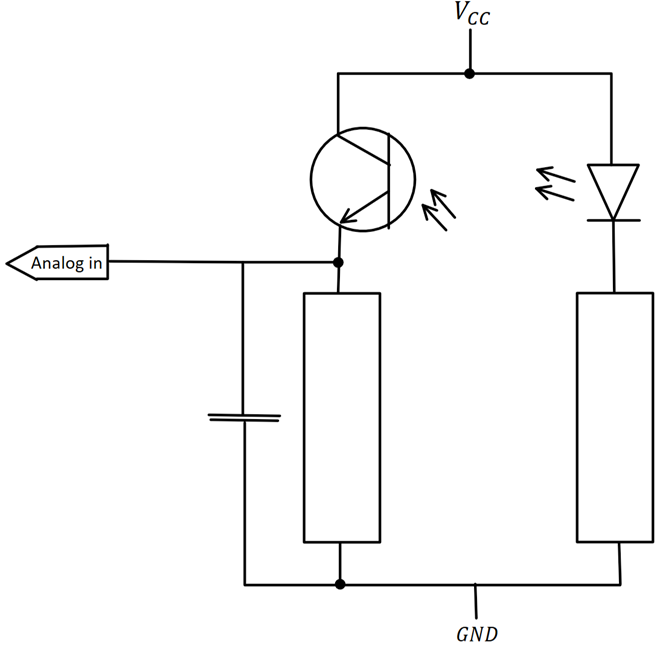
As for now, with the design shown and the video provided showing that we have a relatively stable signal we can measure, which we can convert into distance. As well as creating the design I have assembled three fully complete sensor modules, which we only need to mount onto the bot with the brackets Marte cut out.
When testing the completed sensor modules with the MicroBit we can see that the noise varies by +- 3, which is a relatively small amount when considering all the variables, both within the circuit itself and when considering all the variables when we tested, we decided this was negligible. Such noise amounts to roughly a 0.019V difference from max to min. This could perhaps be removed by taking further steps to filter the signal, though I highly doubt this would give much, or perhaps any, improvements to the read signal. As for now, we will be happy with this and move on to testing the “finished” component to find a way to convert this measured voltage to a distance.
On the motor side, we found that we could remove the downshifting gears of the motors. This will save us a load of space so that the second iteration of the bot will be able to fit, with some margin, within the maze and perhaps even be able to drive diagonally. We have decided that to be able to begin testing the sensors and software as soon as possible, we will not remove the gears for the first prototype as both the wheels and the base plate have been designed considering the motors having the gear housing attached with the wider shaft.
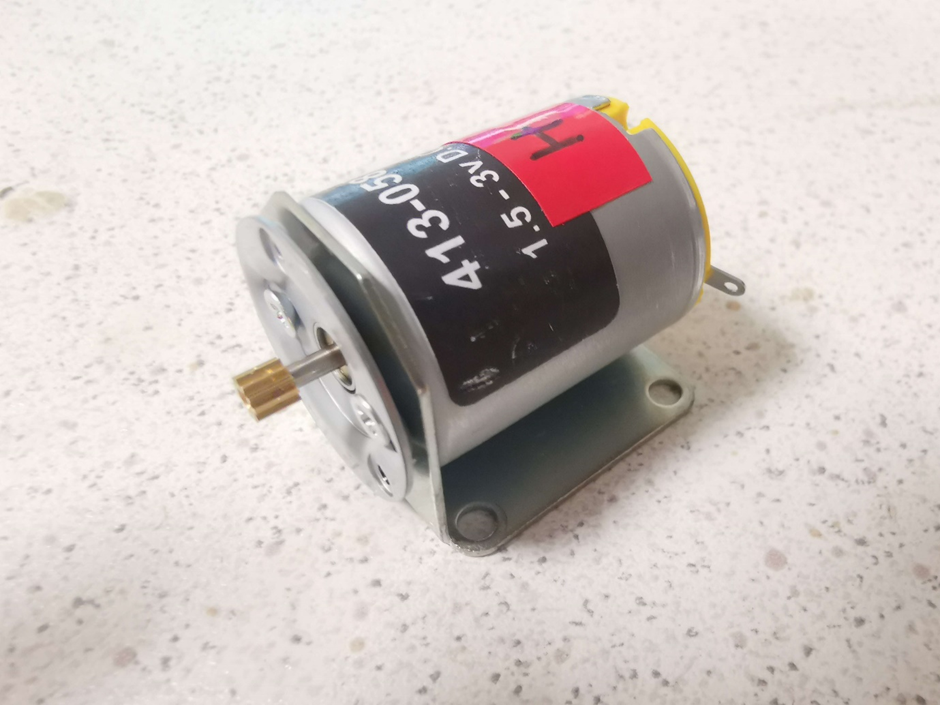
For the foreseeable future, I will most likely be spending my time assisting the Computer Engineers in designing software controllers to ensure that the bot moves as consistently as possible and calibrating the sensors so that we can reliably convert measured voltage to distance.
Bendik
This week I have looked at programming the motors, at different speeds, as well as further developing the IR depth sensors.
The motors need 1.5-3V to operate, and by using PWM, I can send a variety of voltages to the motor driver board. The lower the voltage, the slower the motor spins. Though this sounds simple enough, I found out that when sending lower voltages, there is some instability in the motor speed. It starts out at a certain speed, then spins slower and slower as time passes. So that needs to be solved before we get a working prototype.
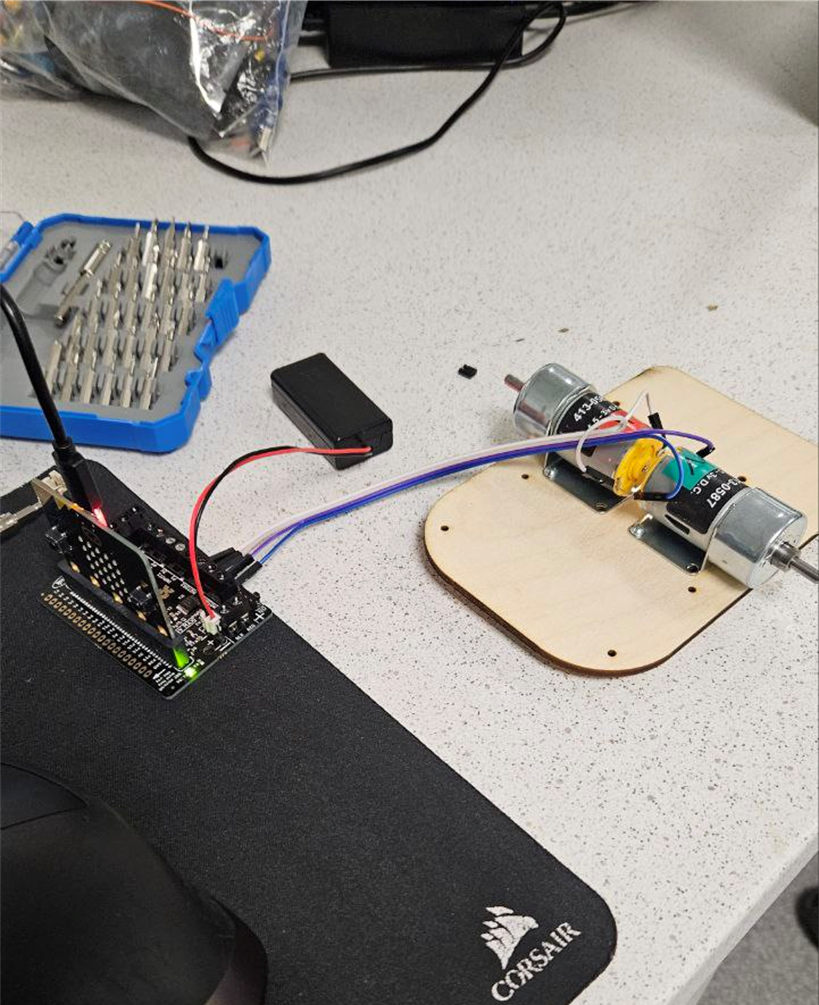
Marte
The MVP is almost finished, remaining to drill two Ø3.8mm holes in the wheels, and it will be ready for testing!
In the upcoming week the MVP will most definitely be finished, and the next task will be to improve the design and/or build the test maze.
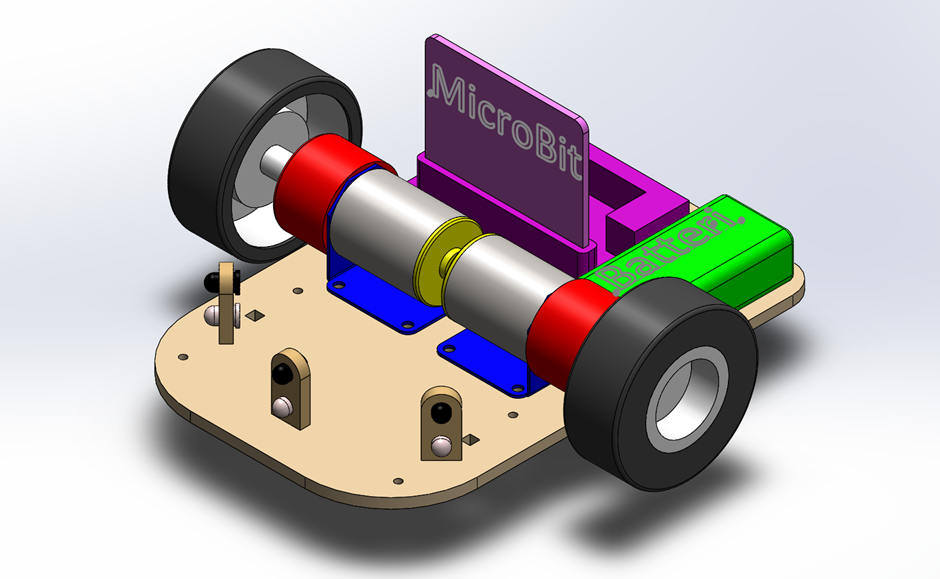
Made some changes to the design, added brackets for the sensors, and removed the big switch board (In reality the switch board is now chopped in smaller parts).
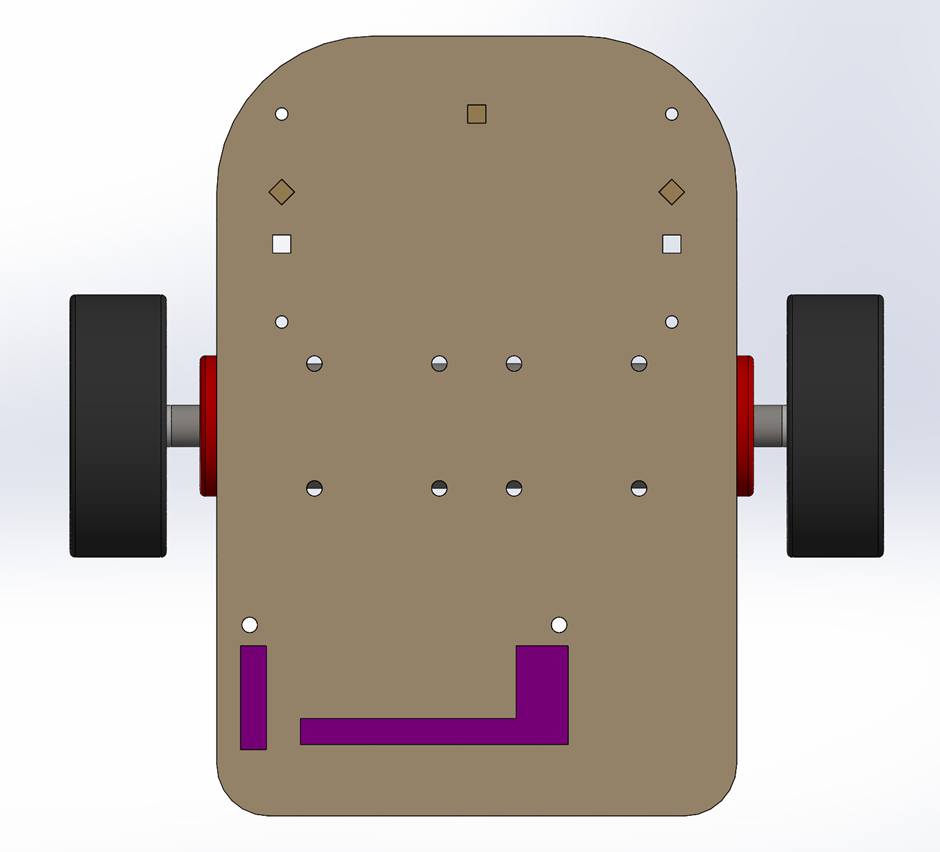
In the front there are two extra squares for testing if the sensors on the sides should have a 45 degree angle or a 90 degree angle.
In the back I cut out an area instead of using washers to make the Kitronik stable when fastened.
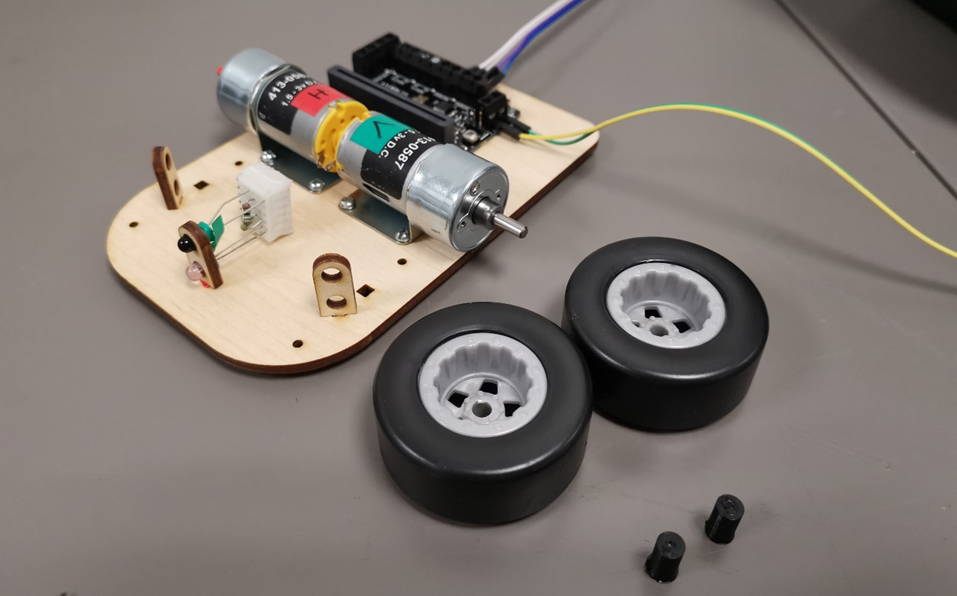
The first attempt on drilling wholes in the wheel to fit the drive shaft failed. I drilled the wholes by hand, and failed to get it axially, resulting in the wheels to get a throw. In addition I only had Ø3.5mm and Ø4mm drill bit, and they made a whole either too small or big for the motor’s drive shaft. After getting tips from Richard, I drilled bigger wholes using a pillar drilling machine and designed a cylinder plug, and Richard 3D printed it.
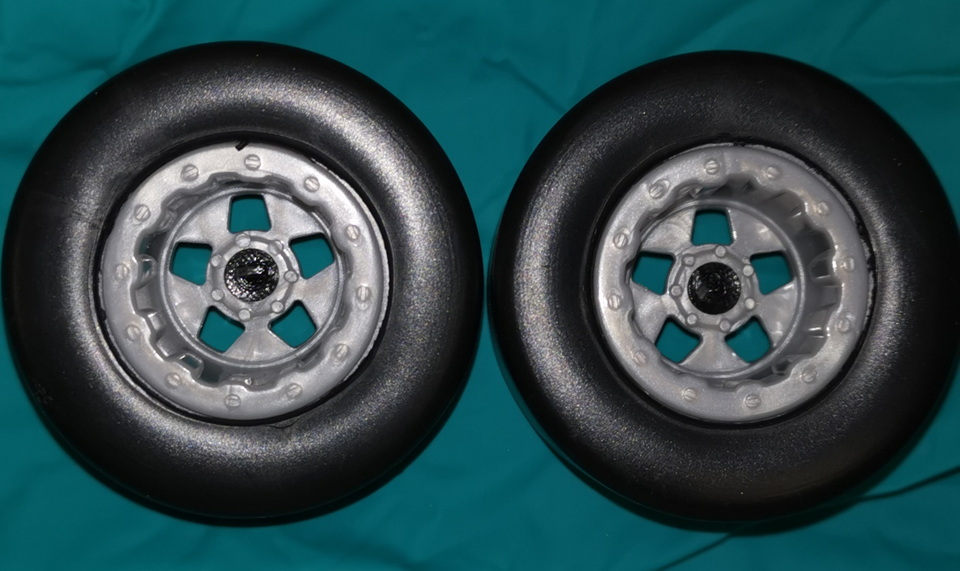
I then glued the plugs to the wheel hub, and they are now ready for a second drilling attempt. I ordered a Ø3.8mm drill bit at Würth, which will hopefully arrive Monday morning. The holes will then be drilled using a lathe for precision.
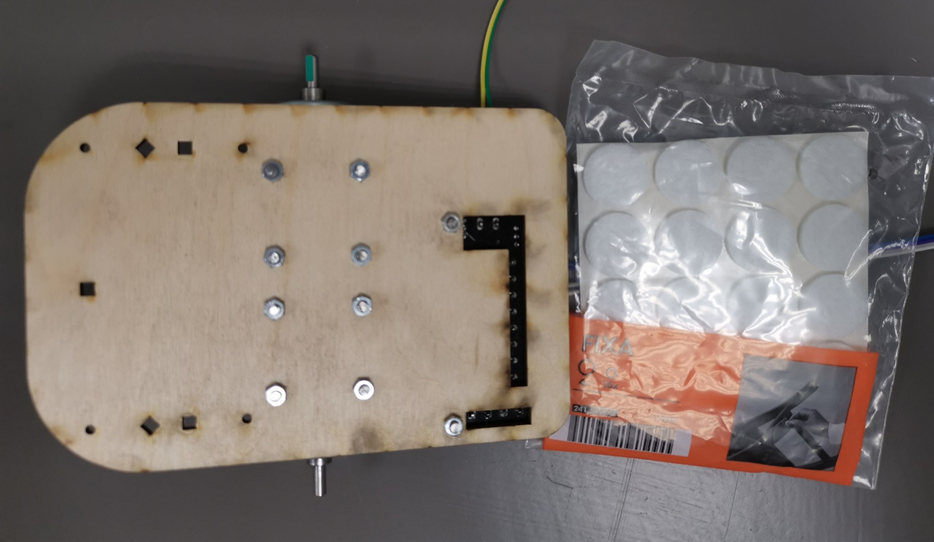
As mentioned in last week’s blog post, the MVP will tip in the back, and we will fasten furniture knobs in the back to see if that solution is sufficient.
Vendel
This week we had hoped to properly assemble the MVP, but due to a snag with the wheels, that could not be completed. Despite that, work has been going well on the IR sensor systems and the motor control aspects.
Overall, I would say we are doing well compared to the requirements of the subject when it comes to time. Not having been able to assemble the car, it’s difficult to build and test the steering and navigation systems, but we should be able to have a working MVP that can drive in a straight-ish line and avoid crashing somewhere in next week.
Having multiple project-based subjects, it’s difficult to focus well on the tasks at hand, but I have tried to at the very least keep the spirits up in the group and engage in discourse and problem solving in meetings. The algorithms for how the mouse should memorize and navigate the maze also need to be made, but with the car not finished, this has had a lower priority to me this week.