This week there have been some changes. We are now four group members instead of five. These are the group members.
- Ilir Bylykbashi – Software engineer
- John Frederick Lærum – Software engineer
- Thomas Frimann – Mechanical engineer
- Daniels Blomnieks – Mechanical engineer
Group weekly reports
Ilir Bylykbashi
Monday 04.09.2023
- Attended lecture and received information on approaches to the project.
- Decided we should try to design the sensing/emitter circuits.
- Decided to use unity for testing our modelling and coding.
- Met up with group to discuss approach for this week.
- Implement a test map and find out the visuals of the micro mouse.
Tuesday 05.09.2023
- Worked with John to create a maze in Unity which we can use for testing.
- Try to implement raycasting for the mouse and sensor to simulate our project.
- Implemented raycasting and virtual sensor information with unity to gather feedback on the distances forward and sides. Wrote scripts on how the sensors should provide feedback.
Onsdag 06.09.2023
- Met up with the group on Teams and discussed the plan for next week and gathered information on what we have done so far on this project.
- Focused on gathering more information about Unity and how we might use Grid to enable the simulation and enable the robot to go forward.
Challenges this week:
Establishing a valid map and grid system in Unity for the simulation.
Summary Ilir:
During this period, I decided to focus on designing sensing/emitter circuits and using Unity for modeling and coding. The computer engineers planned to create a test map for the micro mouse. I collaborated with a team member to build a maze in Unity and implemented raycasting and virtual sensor feedback. I also participated in a virtual team meeting to discuss our project plan and worked on understanding Unity’s Grid system for better simulation and robot movement.
John Frederick Lærum
Spent a lot of time during this week trying to get started on a simulation in Unity.
First part of the week I started by creating the maze I took inspiration from the map used in this video https://www.youtube.com/watch?v=6HuG_72jt6M&t=9s
Then worked on making the object move forward and rotate, also implemented three sensors with Raycast that’s going to represent out IR sensors.
So here’s a topveiw of the maze as it stands now, the goal is located in the center and the starting position of the mouse is bottom left corner where you see the capsule with a camera attached to it that represents our micromouse.
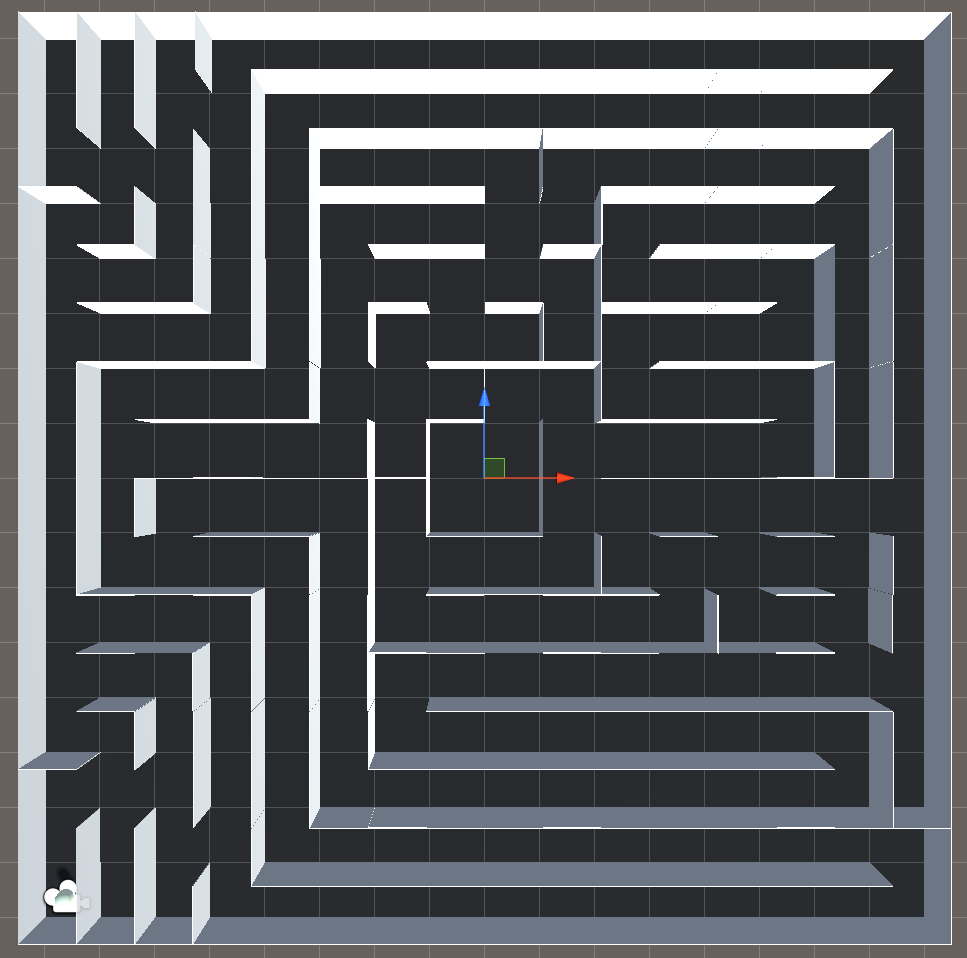
Challenges this week:
It’s a lot to wrap your head around when first starting. For now simple movement, sensing with the sensors and rotation is in place. The challenge now is to combine everything correctly to achieve the two modes “Maze mapping” and “Speed run”.
Thomas Frimann
Monday 04.09.2023
- Team meeting, created a plan for the week
Tuesday 05.09.2023
- Investigated gearing mechanisms and the materials that can be used for the production of belts for drive and transmission from the motor
- Explored the need for wheel bearings and where to source them, as well as their dimensions
Wednesday 06.09.2023
- Concept sketch
- Midweek meeting – created a plan for the upcoming weeks
- Developed a rough plan for the design and when production of parts must commence; the full plan will be completed no later than 13.09.2023
Challenges encountered this week:
- Material selection and how the design should be optimized for maximum efficiency.
Summary by Thomas:
This week, we worked on the concept, created a timeline, and investigated various materials.
Daniels Blomnieks
Monday 04.06.2023
- Group meeting
- Talked about algorithm and driving techniques.
- Sketch to gear down motor even more
- Use of rubber band for gear reduction
Tuesday 05.09.2023
- Talking about what we want to make in solidworks.
- Decided who makes what parts in solidworks
Wednesday 06.09.2023
- Made 3D model of the motor.
- Group meeting
Summary by Daniels
Had a group meeting to discuss how the mouse is going to drive and the algorithm. Discussed also if we want to gear down the motor even more for precision, And also use of rubber band or oring to use for pulley system for gear reduction. We distributed what parts we are going to make. 3d modeled the electric motor.