Mads
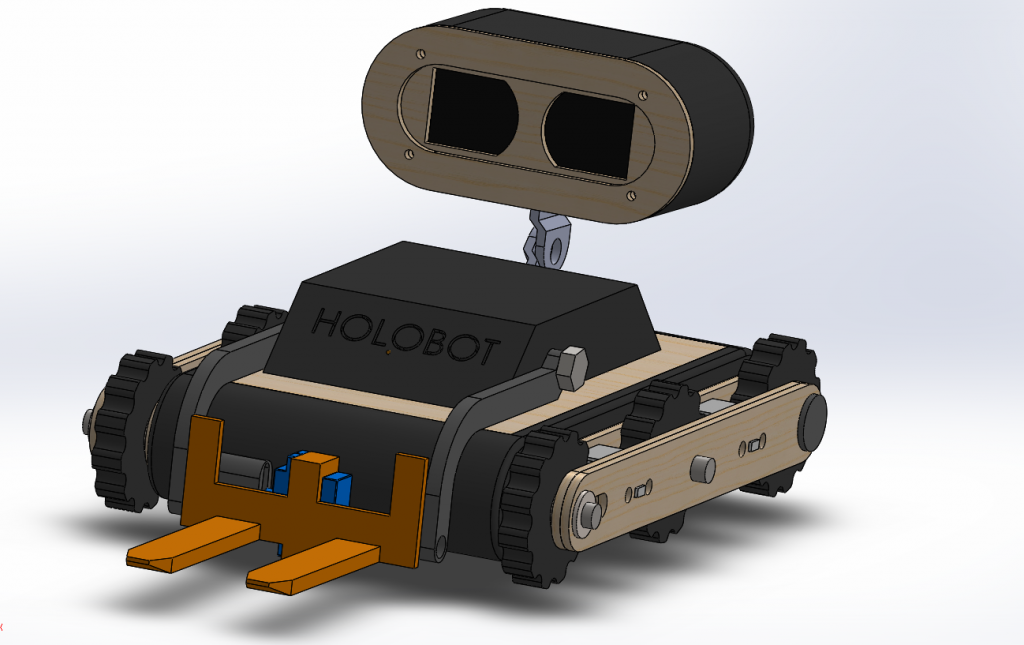
All other exams are finally done and I can resume the Holobot with my full attention. The mechanical and physical are nearly done. The geared DC motors have arrived and are now mounted, they work as intended. This will be a longer blog post which looks back at what I have done the last two weeks.
Tracks
As previously mentioned, I have redesigned and rebuilt the entire track system. The previous one was very little efficient, friction, corners and a very stiff rubber tracks made it so they would barely turn. The new system is fully 3D printed. It consist of 39 small bricks on each track, which are held together by a small string of PLA filament. This is squeezed into the slots, then both sides are melted and pushed flat. This makes the track highly flexible which results in easier turning around the drive wheels. The PLA is more the strong enough for the use, and is also exceptional easy to maintain, repair or replace. To ensure this would be strong enough I have done FEM-analysis on the tracks.
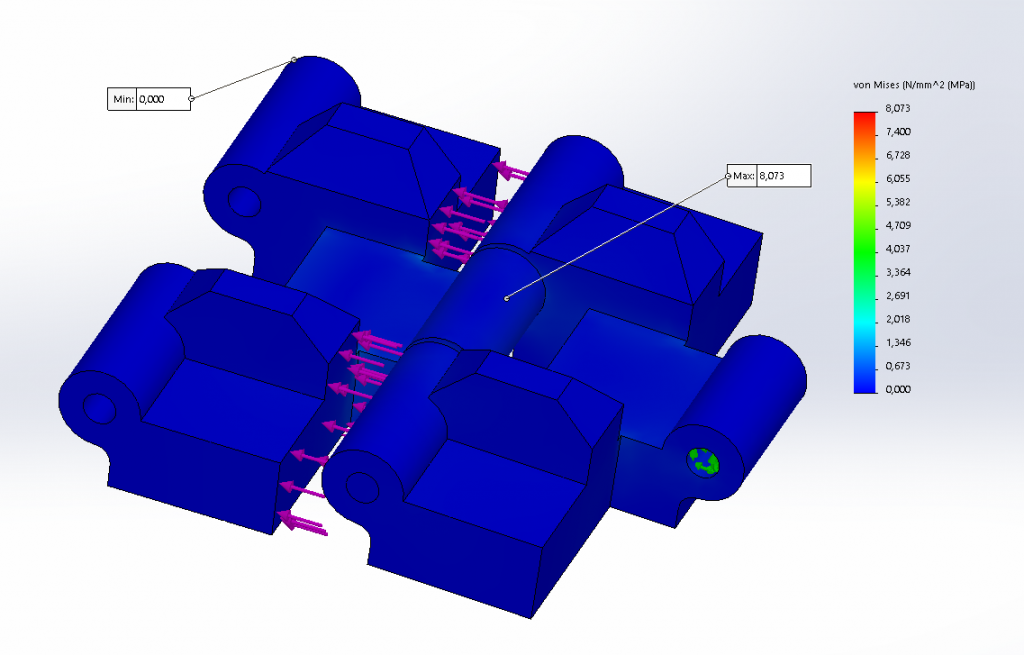
This study is done with the maximum stall torque the geared DC motor will produce at max voltage, 12V. Radius of drive wheel included. Which is only at 2,32N. PLA has a ultimate tensile strength (UTS) around 30-50 MPa, so if we take the average of 40 MPa, this has a safety factor of 5. The bricks and string of filament is more than equipped for the task. If there would be more force applied, the fracture would be on the string of filament in the hinges, which is very easy to replace.
Fork
The arms have been replaced with a fairly easy two axel forklift. Instead of having 4 servos, where two servos lift each arm and two pinch the claws, we now only have 2 servos. Having two servos lifting arms simultaneously is difficult due to jitter, bad potentiometers, plastic gears etc. So with the reduced space the new body has I took the opportunity to make a more efficient lifting system, which will also be more precise. The two arms attached to the body are controlled by one MG995R tower Pro servo. This servo has metal gears, and is rated to 10kg-cm, or 0.980Nm. Which means at the lifting point of the arm which is 0,1m it can lift 1kg. This is plenty as the robot will for the most part only lift a small plywood cube. At the lifting point is a smaller servo, a SG90. This helps keeping the fork vertical while lifting so the object will remain at the correct angle. This smaller servo only weighs 9g, and is a perfect fit here. It can lift 2kg-cm which is more than sufficient due to the short distance to the lifting point.
The remaining time will be spent on polishing the Holobot, making sure every part works as intended. I will help the group as best as I can, starting tomorrow by running various test for the code and electro part. And maybe there will even be time for upgrades!